Overview
ROVNav 6 has been superseded by ROVNav 6+
ROVNav 6 is a 6G Wideband 2 ranging LBL ROV Transceiver and telemetry transceiver specifically designed for installation on work class ROVs.
At a glance
- Use it with Fusion 6G
- Wideband 2 enabled
- High power, long range LBL transceiver
- 3,000, 5,000 or 7,000 m depth rated
- USBL mode for emergency ROV relocation
- Modem mode for harvesting data from Sonardyne sensors
Specifications table
Feature | 8310-3161 | 8310-5261 | 8310-7261 | |
---|---|---|---|---|
Depth rating | 3,000 m | 5,000 m | 7,000 m | |
Operating frequency | MF (20–34 kHz) | MF (20–34 kHz) | MF (20–34 kHz) | |
Transducer beam shape | Omni-directional | Omni-directional | Omni-directional | |
Transmit source level (dB re 1 µPa @ 1 m) | 187–196 dB (4 Levels) | 187–196 dB (4 Levels) | 187–196 dB (4 Levels) | |
Tone Equivalent Energy (TEE) | 193–202 dB | 193–202 dB | 193–202 dB | |
Receiver sensitivity (dB re 1 µPa) | 90–120 dB | 90–120 dB | 90–120 dB | |
Range precision | Better than 15 mm | Better than 15 mm | Better than 15 mm | |
Serial communications (software programmable) |
Primary port | RS232 or RS485 (half-duplex) | RS232 or RS485 (half-duplex) | RS232 or RS485 (half-duplex) |
Secondary port | RS232 or RS485 (half-duplex) or SYNC IN | RS232 or RS485 (half-duplex) or SYNC IN | RS232 or RS485 (half-duplex) or SYNC IN | |
Battery life Li-ion (listening) | 3 days | 3 days | 3 days | |
Operating voltage | 24 or 48 V dc (±10%) | 24 or 48 V dc (±10%) | 24 or 48 V dc (±10%) | |
External power | Active (listening) | <3 W typical (maximum 10 W when charging) | <3 W typical (maximum 10 W when charging) | <3 W typical (maximum 10 W when charging) |
Peak (during transmission) | <80 W | <80 W | <80 W | |
Serial communications connector | AGP (8-way female) |
AGP (8-way female) |
Subconn (8-way female) |
|
Remote transducer connector | AGP (4-way male) | AGP (4-way male) | Burton (3-way male) | |
Housing mechanical construction | Hard anodised aluminium 6082 |
Hard anodised aluminium 7075 |
Hard anodised aluminium 7075 |
|
Remote transducer mechanical construction | Stainless steel 316 | Stainless steel 316 | Stainless steel 316 | |
Dimensions (maximum) (length x diameter) | 768 x 200 mm | 768 x 200 mm | 768 x 200 mm | |
Housing diameter | 134 mm | 134 mm | 140 mm | |
Weight in air/water | Housing assembly | 14.3/5.3 kg | 14.7/5.7 kg | 15.5/6.0 kg |
Transducer | 3.2/2.7 kg | 3.2/2.7 kg | 3.3/2.8 kg | |
Cable (5 m) | 2.7/1.4 kg | 2.7/1.4 kg | 2.7/1.4 kg | |
Sensors | ||||
Temperature (±0.1°C) | Standard | Standard | Standard | |
Strain gauge pressure sensor (±0.1%) | Standard | Standard | Standard | |
High precision strain gauge (±0.01%) | Optional | Optional | Optional | |
Inclinometer (tilt sensor) Range ±90°, accuracy: ±1° (vertical orientation) |
Standard | Standard | Standard | |
Sound velocity sensor ±0.02 m/s accuracy under calibration conditions |
Standard | Standard | Standard |
Frequently asked questions
STP files
Datasheets
Overview
Our range of heavy duty acoustic release frames increase the Working Load Limit (WLL) of RT 6-3000 and RT-6000 acoustic release transponders, enabling you to lift, lower and release heavy loads onto the seabed, including structures and specialist equipment.
The Type 7869-000-01 release frame increases the WLL of a standard RT 6-3000 or RT 6-6000 to 7,500 kg (at 4:1 safety factor) with a breaking load of 30,000 kg. The type 7869-000-05 release frame increases the WLL of a standard RT 6-3000 or RT 6-6000 to 15,000 kg (at a 4:1 safety factor) with a breaking load limit of 60,000 kg.
The Type 7988 release frame has a WLL of 25,000 kg and breaking load of 100,000 kg.
In most cases, both types of release frame can be fitted without any modification to the acoustic release itself and are easily assembled in the field. Manufactured from high-strength steel which is galvanised and powder coated, the releases offer excellent corrosion resistance for long-term deployment.
Applications for which the acoustic releases have been developed include civil engineering, offshore construction, offshore renewables, marine salvage, defence and ocean science.
At a glance
- Working Load Limit of 7,500, 15,000 or 25,000 kg
- Breaking load of up to 100,000 kg
- Choice of depth rating: 4,000 or 12,000 m
- Compact size; just over 1 metre long
- Industry standard lifting rings
Suitable for
- Subsea structure installation
- Research vessels
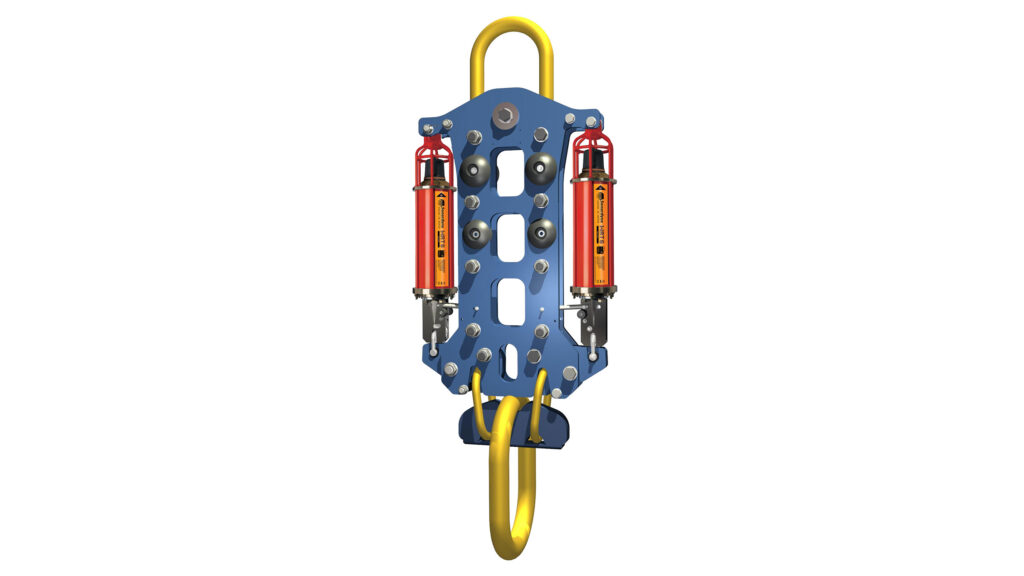
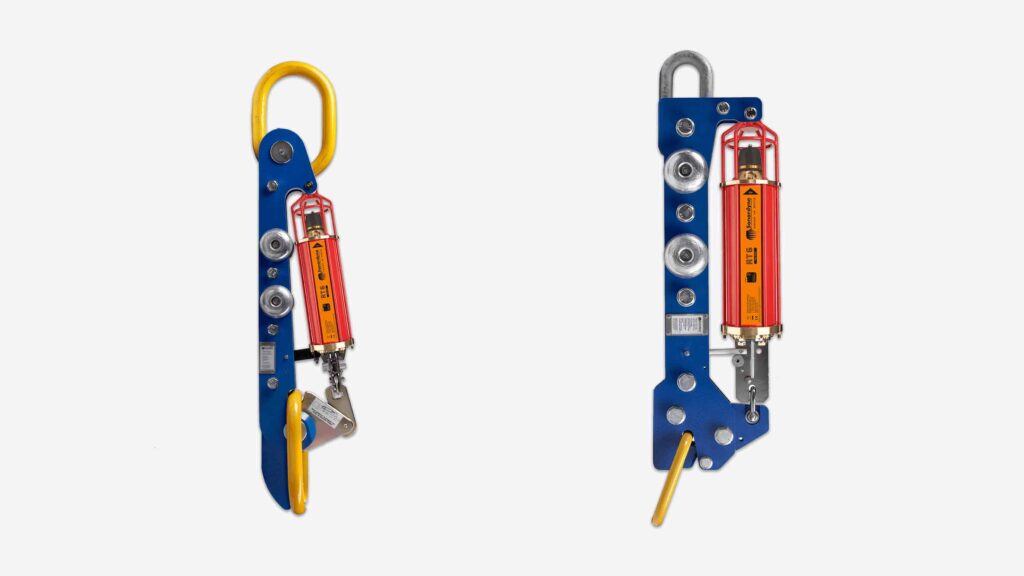
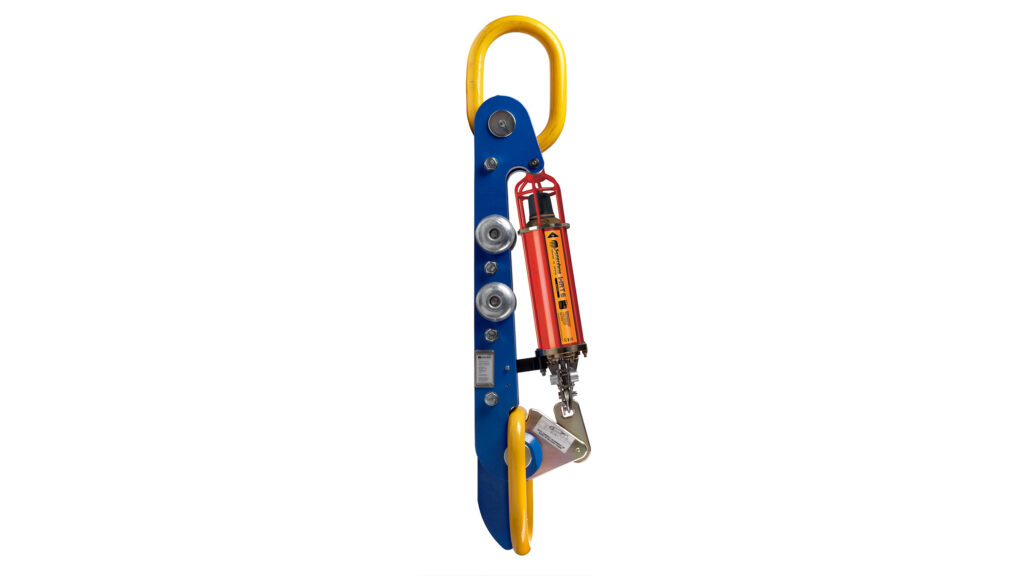
Did you know?
You can use Ranger 2 and Mini-Ranger 2 to release our RT 6 family?
Frequently asked questions
Datasheets
Manuals and quick start guides
Overview
Gyro Compatt 6+ is our combined LBL transponder and AHRS, supporting every stage of your structure installation project. The instrument provides wireless high update rates of attitude, heading, heave, surge, sway, temperature, pressure, SV and acoustic positioning of any subsea object. Deep water structure installation – made easy.
Gyro Compatt 6+ is no longer available for purchase. However, is still available through our hire pool. Contact [email protected] for more information.
At a glance
- Combined LBL transponder and Lodestar AHRS instrument; rugged, ROV deployable design
- Calculates motion and position of any subsea object; use it for structure installation and metrology
- Rechargeable internal battery provides more than a day of continuous use
- Wideband 3 inside; our latest signal protocols delivering fast, efficient operations
- LBL and USBL modes; optimised for Fusion 2 and Ranger 2
- Built to support subsea construction
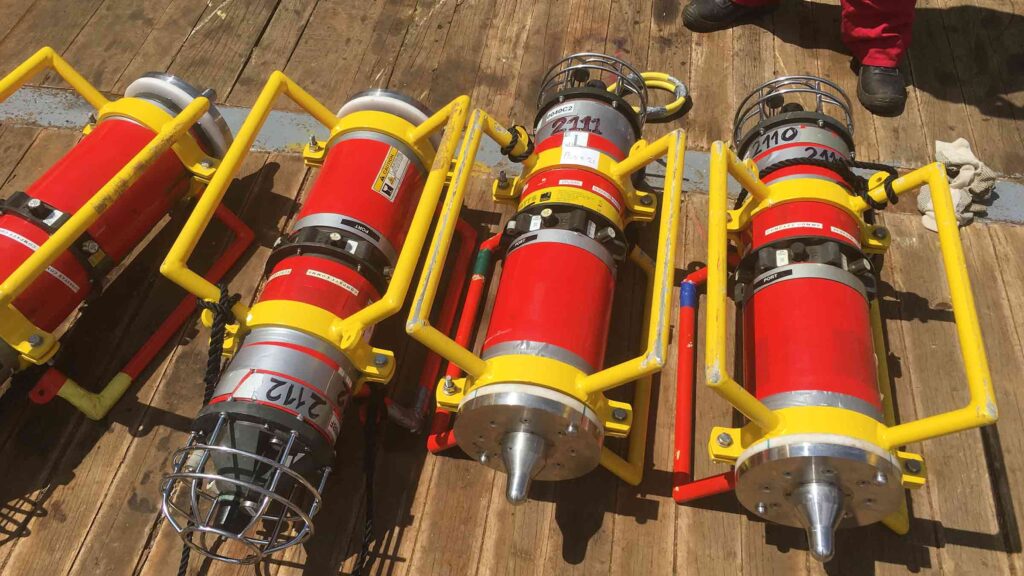
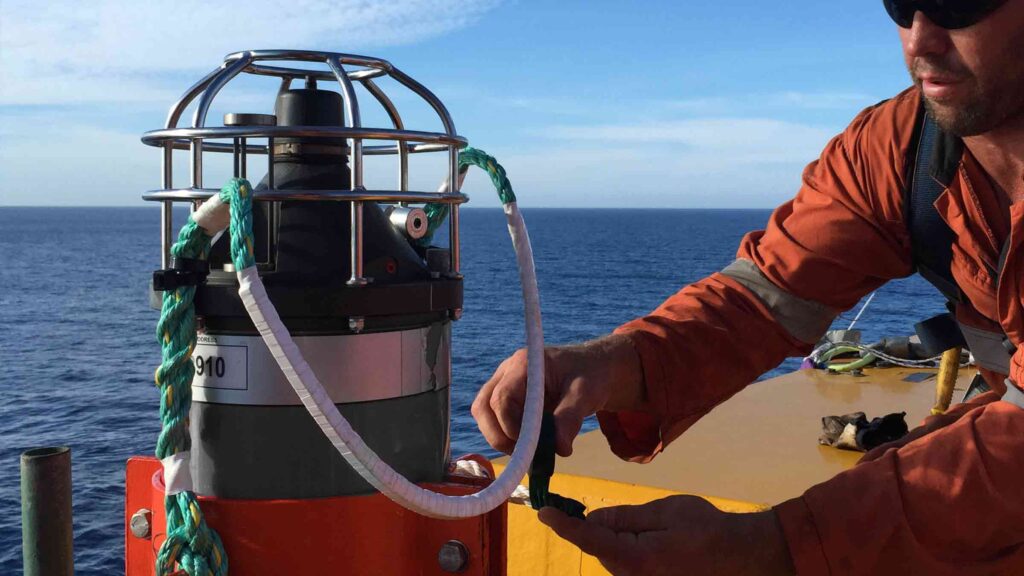
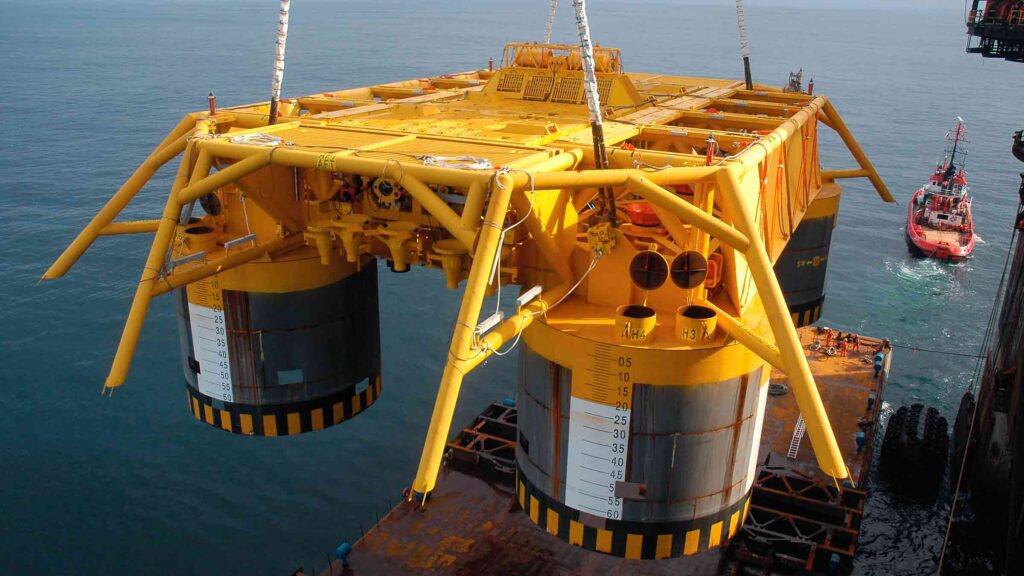
Performance
• Heading accuracy 0.04 to 0.1º Secant latitude
• Ranging precision better than 15mm
• Rechargeable 28 hr internal battery pack
• Simultaneous ranging and sensor data telemetry; requires Fusion 2
• Real time diagnostics on range measurements for quality control
• Autonomous data logging mode
Acoustic, AHRS and Sensors
• MF frequency (19–34 kHz)
• Supports Wideband 3 and Wideband 2 telemetry protocols
• Integrated Sonardyne Lodestar AHRS, factory aligned
• Integrated SV and depth sensors
Design
• Dimensions 918 x 248 mm
• 45/17 kg weight in water/air
• Deploy and recover using ROV
• External AHRS On/Off switch
• Plastic, super duplex stainless steel and anodised aluminium construction. ROHS compliant
Ownership
• What’s in the box: Gyro Compatt 6+, manual
• Warranty: 1 year return to Sonardyne service centre
• ITAR Controlled: No
• UK Export Licence: required; US Export License: covered under de minimis
Specifications table
Feature | Type 8084 | ||
---|---|---|---|
Depth Rating | 3,000 m | ||
Operating Temperature | -5 to +40°C | ||
Storage Temperature | -20 to +55°C | ||
Operational Shock Rating | 22 g, 11 ms half sine | ||
External Battery Pack / ROV Supply | 24 V (20–50 V) | ||
Battery Life | Acoustic Navigation Standby | 3 months | |
Lodestar Permanently Powered On | 28 hours | ||
Acoustic | Compatt 6+ | Operating Frequency | MF (20–34 kHz) Sonardyne Wideband 3 |
Transmit Source Level (dB re 1 µPa @ 1m) |
185–192 dB (5 Levels) | ||
Ranging Precision | Better than 15 mm | ||
Telemetry Protocol | Sonardyne SMS and modem | ||
Ranges Tracked | 14 simultaneous replies | ||
Lodestar AHRS | Heading | Range | 0–360° |
Accuracy | 0.04 to 0.1° secant latitude | ||
Settle Time | <5 minutes | ||
Follow Up Speed | 500° / second | ||
Resolution | 0.01° | ||
Roll and Pitch | Range | ±180° (no physical limit) | |
Accuracy | 0.01° | ||
Resolution | 0.01° | ||
Heave | Range | ±99 m | |
Accuracy (Real Time) | 5 cm or 5% (whichever is the greater) | ||
Bandwidth | User selectable | ||
Resolution | 0.01 m | ||
Digital Output – Output Telegram (e.g. for ROV LED display) | Yes | ||
ROV Switch – Contact Closure | Yes | ||
Data Back-up – Data Logger | 8 GB (expandable to 32 GB) internal memory to allow post processing | ||
Remote Transducer – For ROV Applications, a Remote Transducer is Available | |||
Sensors | Sound Speed Sensor | ±0.03 m/s | |
Pressure – Strain Gauge or Digiquartz | 0.01% FS | ||
Physical | Size (Diameter x Length) | 248 x 918 mm | |
Weight in Air/Water | 45/17 kg |
Frequently asked questions
How to set the latitude on a Gyro Compatt 6
Why am I getting old / incorrect data from my GyroCompatt 6+?
How to turn on a Lodestar Gyro Compatt using Ranger 2 or Fusion 2
I’m outputting a GGA from Fusion 2 / Ranger 2 to NaviPac but the position isn’t appearing in the correct location?
If I’m using Fusion 2, can I choose to use Wideband 2 or Wideband 3 telemetry?
How to plan my sparse LBL array (guidance note)
How do I perform a SLAM calibration in Fusion 2?
How do I perform an LBL calibration in Fusion 2?
Software and firmware
Software and control hardware
Datasheets
Manuals and quick start guides
Using a hammer to crack a nut? Try using a USV instead
USVs are no longer new. They’ve been used in defence for some time now, for a range of tasks from surveillance to mine counter measures. USVs are being used to survey coastal and offshore waters in hydrographic surveys, for ocean science and in oil and gas
The challenge
Crewed vessels used in offshore construction projects are costly and can even hinder progress. But it doesn’t have to be that way. Other sectors that operate in the marine space are now finding new, smaller, smarter, cleaner tools. They’ve been using uncrewed surface vessels (USVs), so the big, crewed vessels can stick to the jobs they’re good at.
So why are we not using them heavily in offshore construction?
One reason may be because offshore construction was in fact an early adopter. But, at the time, there were only a handful of commercial USV operators whose vehicles were just too big for what was needed, making them unwieldy to deploy from an offshore vessel, defeating the point of the exercise.
Another may be the worry of the complexity involved in offshore construction. Creating complex structures on shore is one thing. Creating them under metres of salt water is entirely another.
Then there is the issue of communication and control over the construction process. Making sure each step is taken exactly as planned is fundamental to the overall success of a construction project.
The solution
USV technology has come a long way since their inception. They’ve been used in defence for some time now, for a range of tasks from surveillance to mine countermeasures. USVs are being used to survey coastal and offshore waters in hydrographic surveys, for ocean science and in oil and gas. They’re being used to go out and gather data, either as a platform for oceanographic instruments or by carrying acoustic communications systems to harvest data from sensors deployed at the seabed. You could think of them being like a remote-controlled Dunker.
USVs are now part of the toolbox across a number of sectors and the levels of sophistication and capability are increasing. Worries about lack of control, the complexity of operations or large clunky kit that isn’t up to the delicate tasks required in offshore construction are today unfounded.
In offshore renewables and oil and gas USVs are being used as part of site and seismic surveys, and then through field life, for inspection operations. They’re also being used for maintenance and repair, by acting as deployment platforms for autonomous underwater vehicles (AUVs), remotely operated vehicles (ROVs) and even aerial drones (UAVs).
The results
Today there’s a wide choice of USVs to choose from. From one-man portable USVs to full sized vessels, and on to fully electric coastal systems and hybrid long-range ocean-going vehicles that can operate for weeks on end. The range of commercial models has also grown. You can buy them outright or purchase a data service where you just order the end result – be it data or an inspection campaign.
USVs can now play a central role in construction operations. They can streamline operations and reduce risk for manned offshore construction teams. When deployed they reduce reliance on heavier, costlier tools and free-up crewed assets to be used on elements of a project where they’ll bring more value.
Deepwater structure installation made easy
For five decades, we’ve been working to make subsea developments safer, cleaner and more efficient than ever before. Our aim is always to mitigate risk for our partners, reduce the complexity of deepwater structure installations and increase efficiencies so projects cost less and teams spend less time offshore.
The challenge
When offshore contractor China Offshore Fugro Geosolutions (COFG) approached us looking for ways to improve the installation of multiple deepwater structures, we were excited to support their operation. The project required the installation of four pipeline end terminations. Measuring up to 15 m long, 10 m high and weighing as much as 45 tonnes each, the challenge was to accurately place each structure efficiently and reduce the time needed for the project to be completed.
These kinds of deepwater installations are usually done by installing a gyro frame and placing a subsea gyro into it, with a battery, a modem, sound velocity sensor, and maybe also a depth sensor. These then need to be wired up, turned on, and fingers crossed that it’ll all work. The various connections, components and necessary wiring between each, create multiple opportunities for things to go wrong.
The solution
Gyro Compatt 6 is a compact and versatile positioning transponder with a subsea gyro used to simplify structure positioning. From one instrument everything can be monitored and controlled from the topside using our Ranger 2 6G Ultra-Short BaseLine (USBL) positioning system or Fusion 1 or 2 Long BaseLine (LBL) software. What’s more, it’s quick to recharge on deck, making it a perfect choice for multi-structure installation campaigns.
Onboard the HSYS 201, COFG already use our Ranger 2 USBL positioning system, our Fusion LBL software and a ROVNav 6 transceiver onboard their ROV, all of which work seamlessly with our 6G USBL family of products, of which the Gyro Compatt 6 is a part.
This compact unit is much more than a positioning transponder. The unit combines an LBL transponder Wideband acoustic positioning, Lodestar attitude and heading reference sensor (AHRS), a depth sensor and sound velocity, plus an integrated high-speed acoustic modem. By combining these technologies into one small unit, a single yet highly versatile and easy to install instrument can provide high update rate wireless attitude, heading, heave, surge, sway, pressure, sound speed and acoustic positioning of any subsea object.
There is no need for the traditional gyro frame and subsea gyro technique and all the wiring and crossing of fingers that goes along with it. By deploying the Gyro Compatt 6, ranges from the LBL array can be gathered in real time by a ROVNav 6 LBL ROV transceiver onboard the ROV, and, in turn, tracked in the LBL array.
The results
With just the Gyro Compatt 6 installed and secured for structure monitoring, COFG’s installations were successfully carried out on the Liuhua 29-1 gas field development in water depths ranging from 520 m to 1120 m, between mid-October and the end of November 2019. Each of the four installations was made much easier – with reduced stress, fewer complications and in less time.
Jia Wu, Operation Manager, Engineering Survey Division at China Offshore Fugro Geosolutions (Shenzen) Co. was pleased with how their Gyro Compatt 6 performed.
“This all-in-one system offers us the biggest advantage for the operation, being easier to use, smaller in size and more efficient for preparation,” he says. “It is more convenient to secure as well as recover and does not require wiring between components, compared with a conventional gyro basket (transponder plus battery plus gyro).”
Do you need to simplify a deep water structure installation project? Speak with an expert today.
Shallow water site investigation for offshore wind
From the topside to the underwater instruments, our goal is to make offshore operations easier and less time-consuming, but also highly accurate. As PDE Offshore discovered, with Mini-Ranger 2, our 6G hardware and our Wideband 2 digital acoustic technology onboard, safe and efficient shallow-water site investigation operations, from tracking towfish to positioning seabed geotechnical equipment, are assured.
The challenge
In a short period of time, Taiwan has quickly become a leader in the global build-out of offshore wind. Starting from scratch in 2018, the country has been quick to ramp up its offshore wind capability. Taiwanese company PDE Offshore, based in New Taipei City, was quick to get involved in this new industry and came to us for a USBL system to underpin its offshore wind geotechnical site investigation service offering.
Specifically, it was looking for a system to support geotechnical site and soil investigation works for a new offshore wind farm in the shallow water Taiwan Strait. This involves deploying geotechnical drilling equipment on the seabed at each planned turbine site in just 20 – 60 m water depth. The frame holding the equipment has to be positioned accurately to ensure it’s aligned with the drill string deployed from PDE Offshore’s geotechnical survey vessel.
The solution
PDE Offshore chose a combination of our Mini-Ranger 2 USBL system and our Wideband Sub-Mini 6+ (WSM 6+) transponder/responders to track and position their drilling frame on the seabed. Mini-Ranger 2 is built around the same market-leading 6G hardware and Wideband 2 digital acoustic technology you’ll find in our entire family of USBL systems – even the software is the same.
Critically, it’s designed to easily handle just the kind of shallow waters PDE Offshore had to work in on the project in the Taiwan Strait. At the heart of Mini-Ranger 2 is our HPT 3000, a highly capable surface-deployed USBL transceiver that’s optimised for high performance in shallow water, as well as high elevation and long lay back operating scenarios and data telemetry.
It was a simple choice for PDE Offshore, not least as their onboard surveyor was already familiar with Mini-Ranger 2. What’s more, it’s also a great option for smaller vessels and even unmanned surface vessels (USVs).
A wide range of Sonardyne 6G transponders can be used with Mini-Ranger 2, allowing you to select the most appropriate took for each task. For its operations in the Taiwan Strait, PDE Offshore chose our Wideband Sub-Mini 6+ (WSM 6+) transponder/responders. Designed for positioning ROVs, towfish and other mobile targets in water depths up to 4,000 m, WSM 6+ incorporates our Wideband signal technology, so it offers superior ranging accuracy and fast USBL position updates as well as full two-way Wideband support – interrogation and reply signals.
Targeting
0
GW
by 2025
0
m/s
average wind speed
Average water depth
0
m
for each turbine
The results
PDE Offshore spent summer 2020 performing site investigation works from the MV Geo Energy in the Taiwan Strait. Our WSM 6+s were mounted on the seabed frame and tracked using the Mini-Ranger 2’s HPT 3000, which was deployed on an over-the-side deployment pole from the MV Geo Energy.
Huang Hsin-chih, president of PDE Offshore, says, “Where we work in the Taiwan Strait, water depth is from 20 to 60 meters; in the future, there might be a chance to work in offshore wind farm with water depth from 50 to 200 meters, so whilst we do need a very precise USBL, we don’t need one that’s full ocean depth capable. Through renting, we became familiar with Mini-Ranger 2 and the benefits it brought to our busy geotechnical operations. So it was a simple choice to decide to go ahead and purchase one of our own and it has proven fully capable for our needs on this and future offshore wind projects.”
A SMART deepwater invention
Operations in deepwater are a significant challenge requiring the latest generation of subsea equipment and installation techniques. While the majority of operations do go to plan, there are occasions when they don’t and an innovative approach to deepwater intervention is required.
The challenge
Houston headquartered engineering specialists Trendsetter Vulcan Offshore (TVO) were set just such a difficult deepwater intervention challenge. They were brought in to help an operator rectify a completed wellhead at a deepwater site that had suffered from misalignment. The wellhead, which was in more than 2,000 m water depth, had been bent and there were concerns other components might have been damaged.
TVO were tasked with finding a solution to bringing it back to a vertical position. This would allow intervention access to the well for remediation and abandonment operations, so it could be permanently sealed. A key challenge was to carry out this work extremely carefully and in a controlled manner, in order to prevent any further potential damage to the wellhead.
The solution
TVO came up with an innovative solution to the problem. It proposed a ring of six subsea tensioning systems, mounted on suction piles positioned in a ring on the seafloor around the wellhead. Each one would be connected via a rope to a Trendsetter-supplied lower riser package (LRP) installed onto the wellhead. By carefully tensioning the ropes, they would be able to then bring the wellhead back into an upright position.
To do this in a safe and controlled way, TVO required a monitoring system which would provide:
- Near real-time feedback of the tension data at each of six load pins installed on the LRP (one each for each of the six tensioners).
- Near real-time inclination data from the wellhead itself
Conventional deepwater intervention solutions
Traditionally, inclination data is acquired by visually checking subsea bullseye levels attached to a structure using a diver, or, in this water depth, a remotely operated vehicle (ROV). Similarly, visual displays on the tensioning systems would be the source of the tension data, also read using an ROV.
However, these techniques add a significant amount of time, given the 30-40 m radius of the circle of tensioning systems, even if, as was the plan, only two would need to be actively tensioned during the righting operation. Bullseyes can also be mis-read.
Another alternative option is to deploy battery powered accelerator and inclinometer measuring bottles, using an ROV. But these would have to be retrieved to the surface after each measurement, so would also mean a lengthy operation, potentially taking days.
Taking an alternative, SMART, real-time intervention approach
Instead, TVO proposed and successfully deployed a wireless, intelligent, digital underwater monitoring solution. This provided near real-time inclination and tension data to the operations team at the surface (around three minutes delay). It comprised of two of Sonardyne’s Subsea Monitoring, Analysis and Reporting Technology (SMART) and six Compatt 6 transponders.
The internal inertial measurement unit in each SMART was used to calculate pitch and roll data from two points either side of the LRP, allowing TVO to calculate the wellhead’s bend angle in the local coordinate frame.
This data was then transmitted acoustically, using the SMART’s internal modem, to the surface at three-minute intervals. The Compatt 6s were interfaced with the load cell shackles at each tensioner point on the LRP and transmitted the tension readings to the surface at less than one-minute updates.
Over
0
m
water depth
0
hour
critical righting operation
0
month
continuous monitoring campaign
The results
The righting operation took just three hours, using an ROV to tension the winches at two key tensioning units, one at a time. In comparison, using the alternative methods would have taken days. Throughout, the TVO team and the operator were able to view a constant near real-time visualization of the inclination of the wellhead and the tension that was being applied at each tensioning system. This was done via an internet-based dashboard developed by TVO, so that any member of the wider team, including the operator, from anywhere in the world could watch.
Making a SMART decision
“It was a very unique challenge. There were a lot of studies and approaches analysed within the customer group before making a decision to what the right approach was. They chose ours, using Sonardyne’s SMARTs and Compatt 6s, and it worked very well,” says TVO’s Kim Mittendorf.
“We really could control the two tensioners with the amount of tension we needed in near-real time. While the ROV was tensioning the winch, more than 2,000 m below us, we could see what direction the wellhead was moving in, how the pitch and roll angle changed.
“All the data was also live streamed to a website so that the customer, offshore and onshore, could monitor the operation in near-real time. This drove their decision making and gave them the comfort to continue with the operation as planned.”
Paving the way for a safe well abandonment
Following the righting of the wellhead, the tensioning and monitoring system was kept in place to allow safe intervention and final abandonment operations to be completed. During this phase, the data transmission rates were reduced to once every few hours.
For redundancy, two of the suction piles had relay Compatt 6s installed on them. This was due to a concern that direct line of sight to the transceiver from one or more of the Compatt 6s wouldn’t be possible.
In addition, the ROV had a ROVNav 6 transceiver, as another backup communications pathway. However, none of these were required as the LRP located SMARTs and the six Compatt 6s connected to the load pins were able to directly communicate with the topside transceiver.
Deepwater wireless well intervention success
The entire campaign proved to be a complete success. Thanks to TVO’s engineering and Sonardyne’s monitoring technologies, the operator was able to safely and efficiently decommission this challenging deepwater wellhead.
Initial skepticism from the operator in using a hydro-acoustic approach for data transmission was also overcome and through the success of the project, further confidence has been built into the technology for future applications.
A new world of multi-robot ocean exploration
The OECI’s Technology Integration Challenge made major strides in multi-robot operations, on the surface and underwater, unlocking ways to explore our ocean – and far more efficiently. Find out how and the role our acoustics played.
The challenge
Ocean exploration is costly. Operations involving single underwater platforms, such as remotely operated vehicles (ROVs) or autonomous underwater vehicles (AUVs), often take up an entire cruise. Even when multiple underwater robots can be accommodated on a vessel, only one tends to be deployed at any one time, due to the complexity involved in its deployment, operations and recovery. It makes ocean exploration expensive and limits how much science can be conducted on any one cruise. But what if uncrewed surface vessels (USVs) could be used, not just as force multipliers for mapping operations, but as a remote shepherd, coordinating multiple underwater vehicles, they would be able to operate entirely freely from a mother ship.
This was a key objective of the US’ Ocean Exploration Cooperative Institute (OECI) 2022 Technology Integration expedition NA139 on the Exploration Vessel (EV) Nautilus.
Enhancing ocean exploration through the use of remote and autonomous operations is a key objective of the OECI, a partnership between The University of Rhode Island, The Ocean Exploration Trust (OET), The University of Southern Mississippi, the University of New Hampshire (UNH), Woods Hole Oceanographic Institution (WHOI) and primary funding partner National Oceanic and Atmospheric Administration (NOAA) Ocean Exploration.
The expedition brought together OECI partner robots together with OET’s EV Nautilus for a ground-breaking technology demonstration in the Pacific Ocean during May 2022. These were:
Mesbot – WHOI’s mid-water robot that is designed to image and sample plankton layers.
NUI – WHOI’s hybrid ROV-AUV, designed initially to work under ice, that can operate out to about 20km on a fibre optic cable for high data rate data, but can also continue to operate without the fibre link.
DriX – UNH’s 7 m-long USV capable of supporting a variety of payloads such as multibeam echo sounders, acoustic communications and tracking and surface communications.
Their goal was to have all three platforms operating together, sharing information and situational awareness and relaying their information, via the DriX, back to the EV Nautilus, enabling scientists onboard to remotely control subsurface operations up to 20 km away from the ship.
Key to meeting their goal was inter-vehicle communications, tracking and positioning.
The solution
The DriX used a marine broadband radio link to communicate with the RV Nautilus (and our HPT 3000) to track, position and communicate with (including providing navigation data) the Mesobot and NUI as part of our Mini-Ranger 2 Ultra-Short BaseLine USBL system.
The underwater vehicles Mesobot and NUI were fitted with our AvTrak 6 combined tracking, telemetry and control transponders. The EV Nautilus was also fitted with our Ranger 2 Gyro USBL system, which would have also be able to track, position and communicate with the Mesobot and NUI, if this had been required.
Mini-Ranger 2 is our mid-level USBL tracking system that’s also able to support communications with underwater vehicles. It can track up to 10 targets at a time, at ranges of up to 4,000 m (with an extended range option) and, with our Robotics Pack, enables command and control untethered underwater vehicles.
For the OECI team, it was this combination of communications and positioning – acomms and USBL – that offered the broadest possibilities to the mission, from a single system.
AvTrak 6 is our tracking, communications and relocation transceiver. It allows USBL aiding for your AUV from a surface vessel and robust telemetry for AUV to vessel and AUV-to-AUV communications.
Ranger 2’s Gyro USBL comes pre-calibrated, thanks to its perfectly aligned acoustic transceiver and built-in attitude and heading reference sensor (AHRS), so you don’t need to take the measurements otherwise needed to determine the alignment of the ship’s motion sensors to the acoustic transceiver.
This makes it a very a portable system that the OET can use on vessels of opportunity. On the EV Nautilus, it was fitted through the vessel’s moon pool.
0
robots
0
dives
Communications
0
km
range
The results
“This was a real first for us,” – Professor Larry Mayer, Director of the Center for Coastal and Ocean Mapping, University of New Hampshire.
Over the course of the 16-day expedition near the island of Oahu, off Hawaii, the team tested and demonstrated operational capabilities. Over 30 dives were performed, totaling 210 hours in the water.
The team established a common control system, based on the robot operating system (ROS) for the vehicles and then set out, each time proving out more and more capabilities.
First, they had DriX track and communicate with Mesobot, using Mini-Ranger 2. Because the DriX has GNSS data at the surface, this meant it could position the Mesobot in the real-world and relay this data back to the RV Nautilus.
Next, they sent commands, via the DriX to Mesobot, from EV Nautilus to open and close its samplers, as well as to move up or down or to the right or left as well as change speed through the water column.
But then the most exciting thing happened, explains Professor Mayer:
“Mesobot is designed to sample layers in the water column. But it doesn’t know where they are. DriX has a sonar (EK-80) that could see those layers. So we could get DriX sonar data back on the ship and in real-time see what’s called the scattering layer of plankton and command the Mesobot to go to that layer to sample it.
“Because Drix is circling above, it can actually see the Mesobot in the layer. This was a whole new world. Normally, Mesobot is sampling blindly. We could now direct it into the layer, know it’s in the layer and see if its entrance causes the layer to scatter. All these were unknowns before.”
The team were then able to repeat these activities with NUI, including using DriX to map the seafloor east of Maui and then relay a mission to NUI for further investigation. In addition, CTD data, as well as snippets of imagery and bathymetry were transmitted acoustically up to the DriX, using Mini-Ranger 2, and then via the radio link back to the Nautilus.
“By the end of the cruise we were able to have both vehicles in the water with the DriX circulating above, communicating with each of the vehicles, giving each other situational awareness, and the mothership, it was off do its own thing. I couldn’t have asked for a more successful cruise,” says Larry.
“We are really opening up a new world of multi-vehicle operations. In the old days, we would schedule a cruise and just use the Mesobot or schedule a cruise and just the NUI or an ROV. Even if they would all fit on one ship at the same time, you only use one at a time, so the $60,000 a day would be clicking away and you’re only doing a single science operation.
“Now we can do 2-3 science operations, the efficiencies are tremendous and it allows us to explore the seafloor, water column and surface all at once.
“The Mini-Ranger 2 system gave us the broadest base of possibilities with having both the acoustic communications and the positioning, USBL and acoustic communications, from the same system and that combined set of capabilities was so important to us.
“The standardization and ease at which we were able to send messages across from our programmers made it easy to use. The cooperativeness and responsiveness of the team at Sonardyne was also really helpful. They didn’t see it as disruption, they saw the possibilities.”
The expedition was funded by NOAA Ocean Exploration via the Ocean Exploration Cooperative Institute.
For more information and to watch other videos from Nautilus, click here.
What's possible
You need transponders to be tough, reliable and easy to work with. RT 6-3000 meets these requirements.
Part of our range of acoustic releases, RT 6-3000 combines our extensive mechanical design track record and many years of subsea mooring experience with the flexibility of our 6G platform. The result is an enhanced battery life and, perhaps most significantly, compatibility with our Ranger 2 USBL family.
Deploy. Track. Locate. Recover.
With RT 6-3000, you can use your Ranger 2 USBL to deploy, track, locate and command the instrument – removing the need for a separate topside unit.
If you don’t have access to a Ranger 2 USBL, our rugged and lightweight Deck Topside with an over-the-side dunker is all you need to configure and command your RT 6-3000s.
RT 6-3000s are used to anchor oceanographic moorings to the seabed. However, their compact size and compatibility with Ranger 2 makes them ideal for incorporation into instrument frames or lowered platforms to enable deployment of sub-system packages. Depth rated to 3,000 m, the maximum slant range for operation is dependent on the noise environment and topside used, but ranges to 4,500 m are achievable.
A battery disconnect fob is located on the transducer and uses an internal magnetic switch to electronically disconnect the battery when not in use. This means you don’t have to open the unit to manually disconnect the battery, saving time and reducing the risk of incorrect re-assembly.
Standard features include a Working Load Limit (WLL) of 1,275 kg (at 4:1) and the same trusted spring-assisted release mechanism used on thousands of Sonardyne transponders globally for many years. RT 6-3000 is compatible with our standard tandem and high-load release frames for scenarios requiring a higher WLL.
Speak to us about your requirements as custom frames are also an option.
Acoustics
• Medium Frequency (19-34kHz) band, Wideband 2
• Omni-directional transducer. Track it all the way to the surface
• Sonardyne Wideband 2 signal architecture supporting over 300 unique addresses
• Compatible with any Ranger 2 USBL system and Deck Topside
Design
• 700 x 142 mm, 15 kg weight in water
• Aluminium bronze, duplex stainless steel construction. ROHS compliant
• Configured with iWand hand-held acoustic transponder test and configuration device
• Compatible with our standard tandem and high-load release frame
Performance
• 3,000 m depth rated
• 4,500 m working range
• >32 months battery life; alkaline battery
• 1,275 kg Working Load Limit
• Secure and robust two-way acoustic communications. Only release what you want to release
Ownership
• What’s in the box: RT 6-3000, shackles, manual on USB
• Warranty: 1 year return to Sonardyne service centre
• ITAR Controlled: no
• UK Export Licence: not required
Specifications
Feature | Type 8320-3411 |
---|---|
Depth Rating | 3,000 m* |
Maximum Slant Range | 4,500 m |
Operating Frequency | MF (20–34 kHz) |
Transducer Beam Shape | Hemispherical |
Transmit Source Level (dB re 1 µPa @ 1 m) | 186 dB |
Tone Equivalent Energy (TEE) | 192 dB |
Receive Threshold (dB re 1 µPa) | <90 dB |
Working Load Limit (4:1) | 1,275 kg |
Proof Load | 2,550 kg |
Breaking Load | 5,100 kg |
Maximum Safe Release Load | 1,700 kg |
Battery Life (Alkaline) | >32 months active |
Inclinometer Accuracy | ±5° |
Surface Unit | Deck Topside, Ranger 2 USBL |
Mechanical Construction | Aluminium bronze and duplex stainless steel |
Operating Temperature | -5 to 40°C |
Storage Temperature | -20 to 55°C |
Dimensions (Length x Diameter) | 700 x 142 mm (27.5 x 5.6”) |
Weight in Air/Water | 20/15 kg |
Standards | CE Marked to EN-60945, EN-61010 |
Options | Shallow Water Deck Kit (Deck Topside) – 602-0175 |
Mid Water Deck Kit (Deck Topside) – 602-0179 | |
Heavy Duty Release Frames (7.5 T, 15 T and 25 T) | |
*RT 6-3000 is pressure rated to 4,000 m; however, due to operating range constraints of MF, its use at depths greater than 3,000 m is not recommended. |
Frequently asked questions
What is an Acoustic Release and how does it work?
Why isn’t serial communication available using the iWand in RT 6 Dunker Mode?
6G Terminal Lite Range Test
What is the safe working load for different RT 6 products?
What should I use instead of an ORT and DORT?
How to change the battery on an RT 6-3000 or RT 6000
How to load the release on an RT 6-3000 and RT 6-6000
Which RT 6 is correct for my operations?
How to release an RT 6 acoustic release transponder using Ranger 2
How long can an RT 6-3000 and RT-6 6000 be deployed for?
Deployment
STP files
Software and control hardware
Manuals and quick start guides
Did you know?
RT 6-3000 can be used with our Ranger 2 USBL family or Deck Topside
What is possible
Ranger 2 comes with an impressive list of features including our award-winning 6G (sixth generation) acoustic hardware platform and Sonardyne Wideband 2 digital signal architecture. It provides stable and repeatable acoustic position referencing for your ship’s DP system, including those from GE, Kongsberg, MT, Navis, Thrustmaster and Wärtsilä.
As your needs grow and become more complex, bolt-on software packs unlock additional capability and protect your investment. Take the DP pack and enable your acoustic ranging to be aided by our inertial navigation technology (DP-INS). Add the robotics pack and commanding a swarm of up to 99 AUV’s is at your fingertips.
Ranger 2 can do even more, it also supports robust two-way data telemetry, allowing you to control our range of seafloor deployed, long-endurance sensors and recover your all-important data.
Track everything, in any depth, from any vessel
Why choose it?
- Tracks multiple targets to 11 km;
- Compatible with all makes of DP system – GE, Kongsberg, MT
- System accuracy: when fully optimised it will deliver 0.04% of slant range
- Works with a global inventory of pre-deployed Sonardyne 6G hardware
- Configurations available for USV and temporary vessel installations
- Valuable features included as standard
- Bolt-on packs available for growth with your operations and ambitions
- Developed and supported by a company with over 50 years of experience in innovative underwater technology
Learn more about Ranger 2 USBL
The kit
Transceivers
Our High Performance Transceiver (HPT), is available in a range of different designs to suit your operations whether they are in deep or shallow water or over a long layback.
HPT 5000 / 7000 are acoustic and telemetry transceivers designed for use with Ranger 2 USBL system. HPT 5000 enables targets to be tracked over a wide range of water depths; HPT 7000 is optimised for noisy DP drilling or construction vessels and in deep water.
HPT 5000 offers full hemispherical acoustic coverage so is a popular choice for tracking multiple targets (ROVs, AUVs, towfish, seafloor sensors) over a wide range of depths and elevations. The unit is also suitable for dynamic positioning reference on survey, research and offshore support vessels.
HPT 7000 is engineered for ultra-deepwater operations, tracking targets far below (rather than to the side of) a vessel, and for high vessel noise operating environments such as those typical of DP, drilling and construction where activity from thrusters is liable to cause signal interference.
If you need a solution for a vessel of opportunity, our pre-calibrated, all-in-one Gyro USBL transceiver is perfect. Lighter, smaller and just as capable, our second-generation Gyro USBL transceiver works seamlessly with Ranger 2 to track the position of your subsea targets from a USV, vessel of opportunity or from a pipelay vessel’s stinger over extreme ranges.
- All-in-one instrument; combined 6G acoustic transceiver and AHRS
- Choose between standard or ‘plus’ variants to suit your project’s specifications
- Optimises the performance of Ranger 2; eliminates lever arm offsets, pole bending and ship flexing errors
- Calibrated in-water before delivery – saving you time; install it and go to work
Transponders
The flexibility of the Ranger 2 family is further extended by our range of transponders to support a wide variety of your operations. WMT is a high-power transponder capable of operations to 7,000 m, while AvTrak 6 is our most capable acoustic vehicle instrument, combining the functions of a USBL transponder, LBL transceiver and modem for demanding applications such as AUV command and control.
Discover Ranger 2 in action
A new world of multi-robot ocean exploration
Read moreOptimising shallow water positioning for combined magnetometer and hydrographic surveys
Read moreLong-endurance AUV development with shallow water simplicity
Read morePerformance
• Up to 0.04% of slant range system accuracy
• Up 99 targets tracked, sequentially
• Up to 11,000 m tracking range (LMF)
• 1 Hz position update rate
• Supports all industry standard DP telegrams
• Supports acoustically aided INS
Acoustics
• MF frequency (20–34 kHz) or LMF (14-19.5 kHz)
• Compatible with a wide range of 6G transponders
• Supports Sonardyne Messaging Service for data exchange up to 9,000 bps
• Sonardyne Wideband 2 acoustics for reliable performance in both shallow and deep-water environments
Ownership
• ITAR Controlled: No
• Warranty: 1 year return to Sonardyne service centre
• UK Export Licence: Required
• What’s in the box: HPT 5000 / 7000 / Gyro USBL, deck cables, software, manual
Overview
• Can be used for both survey and construction phases
• Configurable to work in the LMF band enabling you to track targets to beyond 11 km
• Supports complex tracking scenarios such as structures and vehicles with multiple transponders and multiple remote offsets
Specifications table
Feature | Specification |
---|---|
Design | The most powerful USBL system on the market |
Incorporates 30 years of USBL innovation and know-how | |
Recommended for installation on large vessels and USVs | |
Global vessel track record; offshore, research, cable-lay, salvage and naval | |
Shares common platform with other Sonardyne USBLs | |
Performance | Up to 0.04% of slant range system accuracy |
Up to 99 targets tracked, simultaneously | |
Up to 11,000 m tracking range (LMF) | |
1 Hz position update rate | |
Support all industry standard DP telegrams | |
Supports acoustically-aided INS | |
Acoustics | MF frequency (20-34 kHz) or LMF (14-19.5 kHz) |
Sonardyne Wideband 2 digital acoustics for reliable performance in both shallow and deep environments | |
Supports Sonardyne Messaging Service for data exchange up to 9,000 bps | |
Compatible with a wide range of 6G transponders |