HPT 3000
Overview
HPT 3000 is a high performance Wideband 2-enabled Ultra-Short BaseLine (USBL) tracking and telemetry transceiver compatible with our range of 6G transponders.
The transceiver’s acoustic performance is optimised for operations in coastal and near shore where high elevation tracking of targets is often required in low noise environments.
This unit is easy to install on a simple over-the-side pole arrangement enabling a wide range of vessels to take advantage of Mini-Ranger 2 including: anchored barges, small survey craft and uncrewed surface vessels.
HPT 3000 has an internal MTi-30 Xsens sensor which provides pitch, roll and heading data for search and salvage applications which are time critical requiring turn on and track functionality. Shallow water and pipelay from anchor barges also benefit from the internal sensor being calibration free.
The advanced multi-element processing enables transponders to be positioned more precisely, more quickly and more robustly due to improvements in signal processing algorithms. When used as part of a complete Mini-Ranger 2 USBL system, external heading and inertial navigation sensor, class leading performance is achieved.
At a glance
- Use it with Mini-Ranger 2 USBL
- Acoustically optimised for tracking targets in shallow water
- Simple to install on all types of vessel including uncrewed
- Ethernet comms for fast position updates
- Excellent corrosion resistance
‘Discovery Mode’ enables users to automatically detect previously deployed transponders including their configured address and channel, making the system easier to use. The HPT 3000 is a highly capable acoustic USBL tracking transceiver. Its multiple simultaneous channels enable robust tracking of 10 targets.
Manufactured in Aluminium Bronze, the HPT 3000 is intended to be fitted temporarily or permanently to a vessel’s through-hull or over-the-side pole. The full hemispherical coverage optimises performance in shallow water environments boosting transmissions and receive sensitivity in the horizontal axis.
Power and communications are contained in a single cable and because communications transmit from the transceiver to control-room ESH, data rates of up to 100 Mps can be achieved. Ethernet-based communications also enable the unit to interface with your vessel’s existing network for rapid installation.
Mini-Ranger 2 for the next-level USV operations
Read moreL3Harris takes USBL-aided AUV navigation to the next level
Read moreBringing special order accuracy to small diameter AUVs
Read more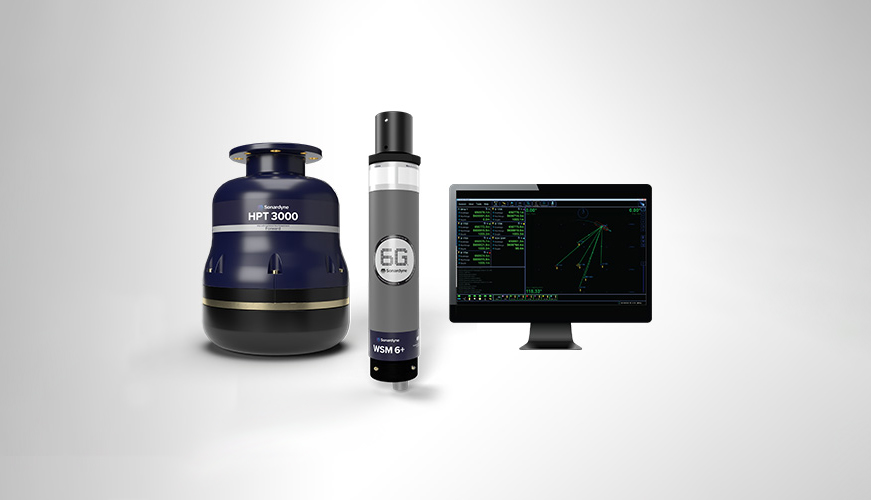
Mini-Ranger 2 USBL
Mini-Ranger 2 is our mid-level USBL target tracking system, perfect for nearshore operations, UXO surveys, search and recovery and structure inspections. With a 995 m operating range, extendable to 4,000 m, it can track up to ten underwater targets simultaneously, including divers, towed instruments, ROVs and AUVs.
Choose to add the Marine Robotics software pack and it will communicate with subsea robotic platforms, sharing positions and exchanging data.
A compact, easily installed system it’s your ideal choice for temporary installation on small survey vessels, as well as USVs.
For the full picture of what your Mini-Ranger 2 USBL is capable of, please visit its dedicated product page.
Specifications table
Feature | Type 8212 | |
---|---|---|
Operational frequency | MF (20–34 kHz) | |
Transceiver performance | Operating range | Restricted to 995 m with Mini Ranger 2 system (4000 m with extended range version) |
Acoustic cover | Full 180° | |
Range precision | Better than 15 mm | |
Positioning repeatability external MRU | All transceivers tested to better than 0.2% of slant range 1 Drms / 0.14% 1 Sigma | |
Positioning repeatability internal Xsens pitch and roll | All transceivers tested to better than 1.3% of slant range 1 Drms / 0.9% 1 Sigma | |
Transmit source level (dB re 1 µPa @ 1 m) | 194 dB | |
Tone Equivalent Energy (TEE) | 200 dB (3 JA) | |
Electrical | 48 V dc (±10%), typical 15 W, maximum 120 W | |
Communication | Ethernet 100 Mbps | |
Operating temperature | -5 to 40°C | |
Storage temperature | -20 to 45°C | |
Mechanical construction | Aluminium bronze | |
Dimensions (height x diameter) | 310 x 234 mm | |
Weight in air/water | 19.4/9.5 kg | |
Note: The absolute accuracy of the system is dependent upon the quality of external attitude and heading sensors, beacon source level, vessel noise, water depth, mechanical rigidity of the transceiver deployment machine, SV knowledge and proper calibration of the total system using CASIUS. |
Frequently asked questions
How to clean a transceiver array face
MF Beacon Positioning for Transition Zone and Ocean Bottom Cable Applications
HPT 2000/3000 Testing
Has anyone ever installed an echosounder and Ranger 2 USBL transceiver directly beside each other? Would this work?
How do USBLs work?
Does the HPT’s main connector need any maintenance?
When to use Depth Aiding
What acoustic address should I use for my USBL transponder
How to interface Ranger 2 into a 3rd party survey system
How can an uncrewed system interact with Ranger 2 software?
STP files
Software and firmware
Software and control hardware
Datasheets
Manuals and quick start guides
Technical bulletin
Did you know?
HPT 3000 is part of our Mini-Ranger 2 USBL system