Author: Nick Swift, Business Manager, Maritime Security
There are more unmanned and autonomous underwater vehicles commercially available today than there has ever been.
They offer huge benefits to marine operations, such as reducing manning and increasing safety and efficiency, in markets from oil and gas and ocean science to hydrographic survey and the military. In the military segment, they’re used for tasks including survey and mine counter measures, or MCM.
Indeed, this week in Glasgow, the use of autonomous underwater vehicles (AUVs) to expand naval and defence capabilities is a common theme at the Undersea Defence Technology (UDT) Conference. Here, they’re able to carry “off-board” sensors and widen operational reach.
As these capabilities increase, as systems become more efficient, cheaper to own and not necessarily that difficult to operate, they’re also starting to be seen as a potential threat. They could, for example, be used for anything from carrying senors for intelligence gathering operations right the way through to carrying explosives.
They could be used to target port-side assets, such as naval or national infrastructure like nuclear power stations, as well as commercial, leisure and military vessels. Think about an aircraft carrier, for example. Someone could program one of these vehicles to be put in the water many kilometres away and direct it into the carrier.
For navies, especially, this is an increasing area of threat; it is an example of technology enabling asymmetric warfare in the maritime domain, increasing the uncertainty about the security of their assets in the marine space.
In UDT’s opening plenary session, Rear Admiral Odd Wein, Head of Naval Systems Department, Swedish Defence Materiel Administration (FMV), described a “grey zone” they see in the marine domain, not least in the Baltic Sea area, a busy, shallow water area. Reducing uncertainty about what is happening in this space, from more normal activities such as search and rescue operations, to actions towards shipping and through to sabotage and full-scale attacks, is important for national security, he said.
Threats need to be detected before they become a danger; they also need to be tracked in order to find out where they are going and therefore where and how the can be intercepted. With this information, asset owners, depending on what the asset is, can decide on an action. For a yacht, for example, that could be to start the engines and move away.
Our Sentinel Intruder Detection Sonar (IDS) was designed as an intruder detection sonar and is equally capable of detecting and tracking AUVs, as well as divers, which present a potential threat to assets or infrastructure.
Operations with Sentinel could even be supported by our multi-aperture side scan sonar Solstice. Solstice was designed for search and classify operations and could be used to periodically survey port or harbour areas for any unexpected objects on the seafloor. This could even be an AUV that has been driven in and then sinks to the seafloor – with an unknown payload.
Get in touch if you would like to hear more about Sentinel or Solstice.
Author: Elaine Maslin, Senior Content Writer and Editor
There’s nothing like starting a new job at the deep end and at Sonardyne that’s quite literally what happened for me.
With my feet barely through the door, I travelled with the team from company headquarters in Blackbushe, Hampshire, down to Plymouth, to join our latest Marine Robotics Week event.
Over three days, we “opened the doors” to our training and testing vessels in Plymouth’s Mayflower Marina to give existing and future clients an in-depth and hands-on look at our marine robotics technology capabilities.
Marine robotics is a fast-growing segment of the marine industry, featuring unmanned surface vessels (USVs) and autonomous or unmanned underwater vehicles (UUV/AUVs), and the systems that connect and control them, which we specialise in.
Plymouth Sound, on the edge of which Mayflower Marina sites, is a challenging environment to operate and demonstrate these systems in, with aggressive tides and different thermal as well as seawater and freshwater layers, all of which make for a tough proving ground for underwater technologies. However, this means those working in the military, oil and gas and ocean science sectors can see our technologies performing in real and challenging conditions – from the comfort and warmth of our vessels.
Our research vessel Echo Explorer took visitors out into the Sound to demonstrate our Solstice side scan multi-aperture sonar.
Solstice, which boasts an impressive 200 metre swath, using only 18 watts, is designed to work on small AUVs operating in stable conditions at a constant depth from the seafloor. For this demonstration, however, it was deployed over the side of Echo Explorer, in fairly rough conditions. Despite this set up, it was still able to pick out details on the seafloor that you would not normally expect to see with a multi-aperture sonar.
Echo Explorer was also used to demonstrate our combined SPRINT-Nav, which houses an INS, DVL and a high precision pressure sensor, in one compact and easy to integrate unit. SPRINT-Nav also performed well within its expected limits.
Meanwhile, onboard Sound Surveyor, our second 12 metre catamaran based at Mayflower Marina, we demonstrated the latest software bolt-on for our Ranger 2 USBL tracking system, the Marine Robotics Pack. Used with AvTrak 6 multi-function transceivers, the Marine Robotics Pack enables tracking and communication with and between multiple subsea targets, such as AUVs or swarms of vehicles, at the same time.
In our static floating classroom, Val B, we focused on BlueComm, our high-speed optical modem. BlueComm can enable high-speed and high-volume data transfer between underwater objects or between underwater and surface based systems, such as an AUV and USV. So how high-speed is high-speed? Well, put it this way, you could transfer HD video with BlueComm, which means subsea survey data could be transmitted to shore far faster than is otherwise possible.
USV supplier and operator ASV Global also joined us to give an on the water demonstration of its C-Cat 3 USV platform, equipped with our Syrinx DVL. As well as providing bottom-lock navigation aiding, Syrinx’s ADCP mode was used to show how a water column can be profiled “on the go”. The sight of an unmanned yellow craft manoeuvring between private yachts certainly caught the eye of many other marina users during the week.
Many of our visitors were impressed that we were happy to demonstrate our technologies in far from ideal environments (including a very windy and quite wet day one).
Our visitors were also impressed with the range and the capabilities of technologies demonstrated and the breadth and depth of knowledge the staff we had on site to talk them through the various systems (as well as a tasty lunch in the on-site restaurant).
The event was also a chance for us to show off our Plymouth Sea Trials and Training Centre facilities at Mayflower Marina, which are available to hire. Indeed, all our vessels, their crew and instrumentation, can be hired, supported by permanently installed LBL and USBL equipment on site.
Most importantly, the event was also a chance for us to meet our clients, to discuss how we can help them and to adapt our technologies to meet their needs, and for our visitors meet us and other visitors.
Ioseba Tena, Global Business Manager for Marine Robotic Systems, led the event. He said: “It’s about the opportunity to have time to talk to our customers, understand their requirements and see how we can adapt our solutions to meet their requirements.”
Marine Robotics Week was our third marine robotics demonstration event. We hope to hold more and are planning the next one, which will be outside the UK. Let us know if you would like to attend a future event and don’t just take it from us how useful these events are. Watch our short film from the event to see for yourself.
Author: Edmund Ceurstemont, USBL technical authority
In July last year I reported on the trials we performed off California (Part 1) to demonstrate the impressive tracking performance of our Lower Medium Frequency (LMF) Ranger 2 Ultra-Short BaseLine (USBL) system. In November we journeyed to the Spanish island of Tenerife – this time to characterise the long range data telemetry performance of the same system.
As a location to conduct trials of marine technology and science platforms, Tenerife and California share at least one thing in common; the ability to access very deep water, very quickly from within a short transit from port. So it’s no surprise that the UK’s National Oceanography Centre (NOC) regularly choose the island to conduct routine equipment tests from.
RRS James Cook–a model vessel
Hosting us for the latest round of our LMF USBL experiments was the Royal Research Ship RRS James Cook. Although the ship celebrated its 10th birthday in 2016, it is still among the most modern research ships currently in service and has been used as a model for many other ocean-going research ships, including several used by Chinese institutes.
Our Medium Frequency (MF) USBL systems are popular for tracking targets and dynamically positioning a vessel in a few hundred metres down to a few thousand. However, when you need to reach full ocean depth or track a towfish over a very long layback, a common need of the ocean science community, then it’s time to consider LMF.
Outwardly, an LMF Ranger 2 USBL is similar to an MF system. But instead of operating in the 19 to 34 kHz frequency range, the vessel mounted transceiver and transponder hardware is built to work from around 14 to 19.5 kHz. This subtle shift halves absorption by the water path, meaning acoustic signals travel further. It can also mean the system is more susceptible to noise interference from the vessel itself. But, as these trials would go on to show, the gain in received signal as a consequence of less absorption, more than compensates for additional vessel noise in the LMF band.
For maximum operational flexibility, the RRS James Cook is permanently fitted with our MF HPT 5000 and HPT 7000 transceivers on her twin USBL spars. This setup presented us with the ideal opportunity to temporarily swap out the HPT 7000 unit with the LMF variant (HPT 7000L) in order to compare it with MF performance in near identical conditions and configuration. The one caveat to this being HPT 5000 has a smaller array giving a wider beamwidth with less noise rejection.
With the HPT 7000L fitted, a calibration procedure to correct for lever arms and installation offsets was conducted using an omnidirectional Compatt 6 transponder deployed to a depth of 4,400 metres. This produced a calculated slant range error of 0.14% (1 DRMS)– similar to the 0.12% achieved during our Californian trial. In practical terms, this means that when tracking a target 11,000 metres away, 66% of position fixes should be within 15.4 metres.
With the system calibrated and noise measurements made, a series of tests were carried out with the ship steaming away from the Compatt on different courses in order to average out the impacts of environmental conditions. Analysis of these runs again echoed previous trials data with consistent tracking achieved out to a slant range in excess of11,000 metres. Switching to a Compatt with a higher power directional transducer would yield even greater ranges.
Telemetry schemes
The next test involved putting LMF through its telemetry paces over two slant ranges of 4,300 and 7,200 metres to a LMF Compatt 6 which was fitted with a directional transducer.
Our 6G (Sixth Generation) family of instruments support seven data rate telemetry schemes, ranging from 200 bps up to a nominal maximum of 9,000 bps. All support transmission of the different telemetry schemes however only multi-element platforms, such as our USBL transceivers, support two of the most robust, high-speed telemetry schemes of 3,000 and 6,000 bps due to their enhanced encoding.
Actual rates achievable are dependent on configuring the delays between packets to minimise errors and consequent retries, which in turn reduce real-world data-rates. The tests were carried out with a default set of delays which are normally used to allow the remote modem time to buffer external data using our different schemes. Actual data rates (including re-tries) were observed in excess of 5,000 bps over a slant range of 4,300 metres at 8 millijoules per bit, and in excess of 2,000 bps over a slant range of 7,200 metres at 17 millijoules per bit.
These results serve to underline how Ranger 2’s impressive ‘out-of-the-box’ positioning and telemetry performance in the MF band reaches new levels of capability when switching to LMF . For anyone taking on the challenges of the deep ocean, LMF is a key enabler for their vessels and has the flexibility to meet their precise in-water and near-bottom sustained observation needs.
This is because LMF not only supports control of deep AUVs and long range towfish tracking, but as these trials have shown, is also highly efficient at harvesting data from a wide range of compatible Sonardyne 6G LMF long-life seabed instruments, LMF telemetry therefore unlocks the full potential of these systems by enabling access to the critical data that they are capable of collecting over deployments, which can be several years’ long.
If you have any questions or would like to run through any of the trial in further detail, please get in touch, I would love to hear your thoughts.
Vancouver-based Cellula Robotics Ltd has successfully demonstrated the capabilities of its Imotus-1 hovering autonomous underwater vehicle (HAUV) for inspection and data acquisition missions in confined environments.
During a week of testing at a pool facility, Imotus-1 navigated using proprietary Simultaneous Localization and Mapping (SLAM) algorithms to hold station, waypoint track and manoeuvre around obstacles.
An autonomous docking demonstration, sponsored by Ocean Networks Canada, included high bandwidth wireless communications between Imotus and its docking station using a pair of our BlueComm 100 optical modems. The technology is considered to be a critical risk reduction tool for future open water applications, enabling user monitoring and potential intervention in the docking process.
Scott McLean, Director of Ocean Networks Canada, said, “This was an excellent demonstration of Canadian technology that has broad applications globally for both industry and research. Demonstrating both wireless optical communications and contactless connectors for charging and high speed communications, is an essential step to creating the next generation in hybrid AUV systems.”
To see the Cellula in action with BlueComm, watch the video below:
Author – Jose Puig – Regional Sales Manager – Asia
Surprisingly, it was a mild weekend in early March that welcomed the student teams participating in annual Singapore AUV Challenge (SAUVC), organized by the IEEE OES Singapore with support of the National University of Singapore and Singapore Polytechnic.
The arena for the fifth running of the competition was the Singapore Polytechnic training pools, an outdoor venue with a full size Olympic distance swimming pool and two smaller splash pools.
The larger of the splash pools served as the practice arena for the AUVs brought to compete by the more than 25 participating universities from 10 South East Asian countries; Thailand, Singapore, Russia, Malaysia, Pakistan, Sri Lanka, India, Indonesia, China and Bangladesh. The main competition was held in the Olympic pool.
The SAUVC competition challenges student teams to design and build an AUV which can perform simulations of four tasks that ‘real world’ operational AUVs would be expected to perform; AUV navigation, visual identification, acoustic localisation and robotic manipulation.
To decide the winner of the competition, points are awarded by a panel of judges for the speed and accuracy at which the AUV performs each of these tasks.
The event was held over four days from the 9th -12th of March 2018. The first day was team registration, welcome address, safety briefing, overview of the completion rules and regulations and then team practice and test runs.
Day two held and further practice runs and qualification rounds. On day three the qualifying teams entered the completion rounds where the three finalist were determined.
The final day of the event saw the guest speaker presentations, amongst them Tom Curtin from the University of Washington and William Kirkwood of the Monterrey Bay Aquarium Research Centre. The event closed with a gala dinner and prize presentation ceremony.
The competition was fierce and very close, however the victory went to the Intelligent Marine Vehicle Team (SAUVC-CN-01) North-western Polytechnic University of Xi’an, China. Runners up were the Tiburon (SAUVC-IN-12) team from NIT Rourkela of Rourkela, India, followed by team FEFU/IMTP (SAUVC-RU-01) from the Far Eastern Federal University in Vladivostok, Russia. Congratulations to all!
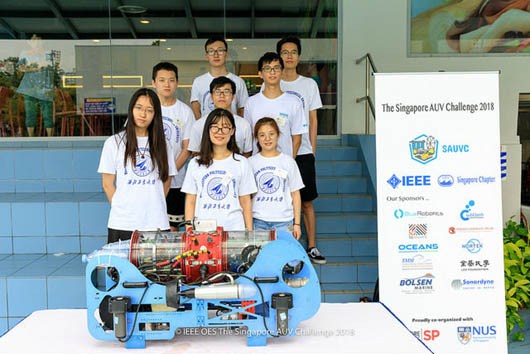
Intelligent Marine Vehicle Team (SAUVC-CN-01) North-Western Polytechnic University of Xian China
As a business, we’re committed to developing not only the next generation of subsea technology, but also the next generation of subsea engineers that are responsible for those products. Events like these are crucial, and we were proud play a small part by helping to sponsor SAUVC 2018. We look forward to both the temperature and the competition hotting up in 12 months time!
Allseas, a global leader in offshore pipeline installation and subsea construction, is to take advantage of the performance and operational benefits available from Sonardyne International’s GyroUSBL acoustic positioning technology, following an order for two systems for its 236 metre long lay vessel, Lorelay.
Used in conjunction with a Ranger 2 USBL (Ultra-Short BaseLine) topside which also formed part of the order, the GyroUSBL transceivers will be installed on the end of the Lorelay’s stinger to acoustically track an ROV deployed to ensure a pipe is accurately touching down in the permitted corridor.
USBL transceivers are routinely deployed through the hull or over-the-side of a vessel, enabling targets to be tracked below, to the side and far behind. However, on a large DP pipelay vessel such as the Lorelay, a transceiver cannot reliably ‘see’ through the thruster wash created at the rear so touchdown monitoring operations are often conducted by an ROV operating from a survey vessel (equipped with its own USBL system) following on behind. With a stinger-mounted GyroUSBL, there is a proven alternative.
The unit combines a 6G HPT transceiver (either 5,000 or 7,000 model) and Lodestar Attitude and Heading Reference System in the same assembly and is supplied pre-calibrated to eliminate the mechanical alignment errors seen in conventional USBL setups. These features allow an acoustic transceiver to be sited well away from noise interference, even on a dynamic structure such as a stinger, and deliver outstanding positioning performance. It also means that a pipelay vessel is able to employ its own ROV to carry out touchdown monitoring, allowing the accompanying survey vessel to get on with another task, or eliminating the need for it altogether.
Mounting a GyroUSBL on a stinger is now a widely adopted practise amongst pipelay vessel operators, with the technique having first appeared on the market in 2013. The Lorelay will be third vessel in the Allseas fleet to be equipped in this way, with systems already in operation on the Audacia and Solitaire.
[blockquote author=” Alan MacDonald, Sales Manager at Sonardyne in Aberdeen “]”Locating a transceiver on the stinger is a great solution for ensuring that vessel noise disruption is rejected. The time-saving features of GyroUSBL results in reduced operational costs with the ability for users to move it from vessel to vessel with minimal downtime whilst maintaining the highest levels of positioning performance.”[/blockquote]
Global subsea equipment specialist, Ashtead Technology has selected acoustic and inertial navigation technology from Sonardyne International Ltd. to add to its rental fleet. The multiple SPRINT-Nav systems will be made available to support survey and construction projects using ROVs and AUVs in water depths down to 4,000 metres.
SPRINT-Nav makes optimal use of acoustic aiding from data sources including USBL, sparse LBL and DVL and pressure sensors to improve the accuracy, precision and reliability of subsea vehicle navigation. Its all-in-one design tightly couples Sonardyne’s SPRINT inertial and Syrinx Doppler technologies to enable marine robotic platforms to remain precisely on course over many kilometres travelled, even if one or two DVL beams become unavailable.
The compact design of SPRINT-Nav’s titanium subsea housing is considered to be one of the smallest instruments of its type on the market. This ensures rapid and simple mobilisation on vehicles and an ideal choice for rental projects.
[blockquote author=” Ross MacLeod, Technical Director of Ashtead Technology “]”Our existing pool of acoustic and inertial navigation systems from Sonardyne have proven to be extremely popular with our customers and we have enhanced our rental fleet to meet their growing demands. This investment underlines our commitment to the subsea market, by offering the latest, most efficient technologies available and will see our clients experience a more cost-effective, reliable solution.”[/blockquote]
Dan Zatezalo, Sales Manager with Sonardyne said, “We’re delighted that Ashtead is the latest organisation to take delivery of SPRINT-Nav systems. We’re seeing more and more field development specifications around the world calling for our hybrid navigation solution which ultimately translates into projects being completed in less time and for less cost.”
Limited by space, layout or weight? Don’t worry; our most popular navigation, tracking and modem products are now available in OEM form meaning you can package them in any way that best suits you.
Lodestar AHRS OEM/ SPRINT INS OEM (obsolete)
Our 3rd generation Lodestar and SPRINT mechanics addressed many users’ needs for a smaller and lighter form-factor. But sometimes, a vehicle such as a USV or AIV are so restricted on payload capacity, further size and weight savings need to be made. This can now be achieved with an OEM Lodestar or SPRINT. The lightweight aluminium housing of the SPRINT 500 model shown here measures just 202mm in diameter by 162mm tall.
Nano AvTrak 6 OEM
Small AUVs need small instruments and they don’t get much smaller than our new Nano AvTrak 6 OEM. It measures just 87.7mm long and 56mm wide but we’ve managed to pack in many of the features supported by the larger AvTrak 6 transceiver including; USBL tracking and two-way comms. A remote transducer gives you the flexibility to mount it anywhere, whilst the li-ion battery gives you 10 days standby life to help you recover the vehicle if it’s lost.
Syrinx DVL OEM
Syrinx is our 600 kHz Doppler Velocity Log (DVL). When fitted to your subsea vehicles and surface platforms, it’s capable of high altitude navigation that’s comparable to a 300 kHz DVL with the high resolution performance of a 1200 kHz DVL. In OEM form you will get a full depth rated, water blocked array that’s connected by cable to a separate electronics module. You can package this into your vehicle’s existing main subsea electronics, or re-package it in an entirely custom housing designed to meet your operational setup.
AvTrak 6 OEM
The lightweight rechargeable transceiver design of AvTrak 6 OEM allows for easy integration into autonomous vehicles and provides all of the features supported by the standard AvTrak 6 including; Sparse LBL ranging and Burn Wire. The OEM chassis can be customised to provide mounting points for specific vehicle internals and is supplied with a threaded boss mount MF Omni-directional transducer for easy mounting on a vehicle’s hull. The integrated li-ion rechargeable battery provides up to 30 days emergency standby life.
If you would like any more information on any of the products here, please get in touch with your local Sonardyne office.
Author: Ioseba Tena – Global Business Manager – Marine Robotic Systems
I keep telling everyone that’ll listen that now is a great time to be working with ocean robots. And, judging by OI 2018, it will only keep getting better. It’s not any one type of ocean robot that’s doing well, it’s all of them. Spurred by difficult economic conditions in the offshore industries and hoping to exploit resources with much finer margins, like fisheries or renewables, the industry is no longer just evaluating more autonomy. We are now using it commercially.
Everything Remotely Possible
I was impressed with the technology being integrated into observation-class ROVs. It used to just be a camera, now it’s common to see a multi-beam, a USBL, a DVL and even INS mounted on them. Obviously, I need to bring up the work we did at the dockside with our newly launched, very portable Micro-Ranger 2 USBL system. We used it to track the small VideoRay Pro4 and managed to demonstrate great accuracy in very challenging conditions. This is great. It means even the smallest form factor systems can be tracked. It’s not just a video anymore.
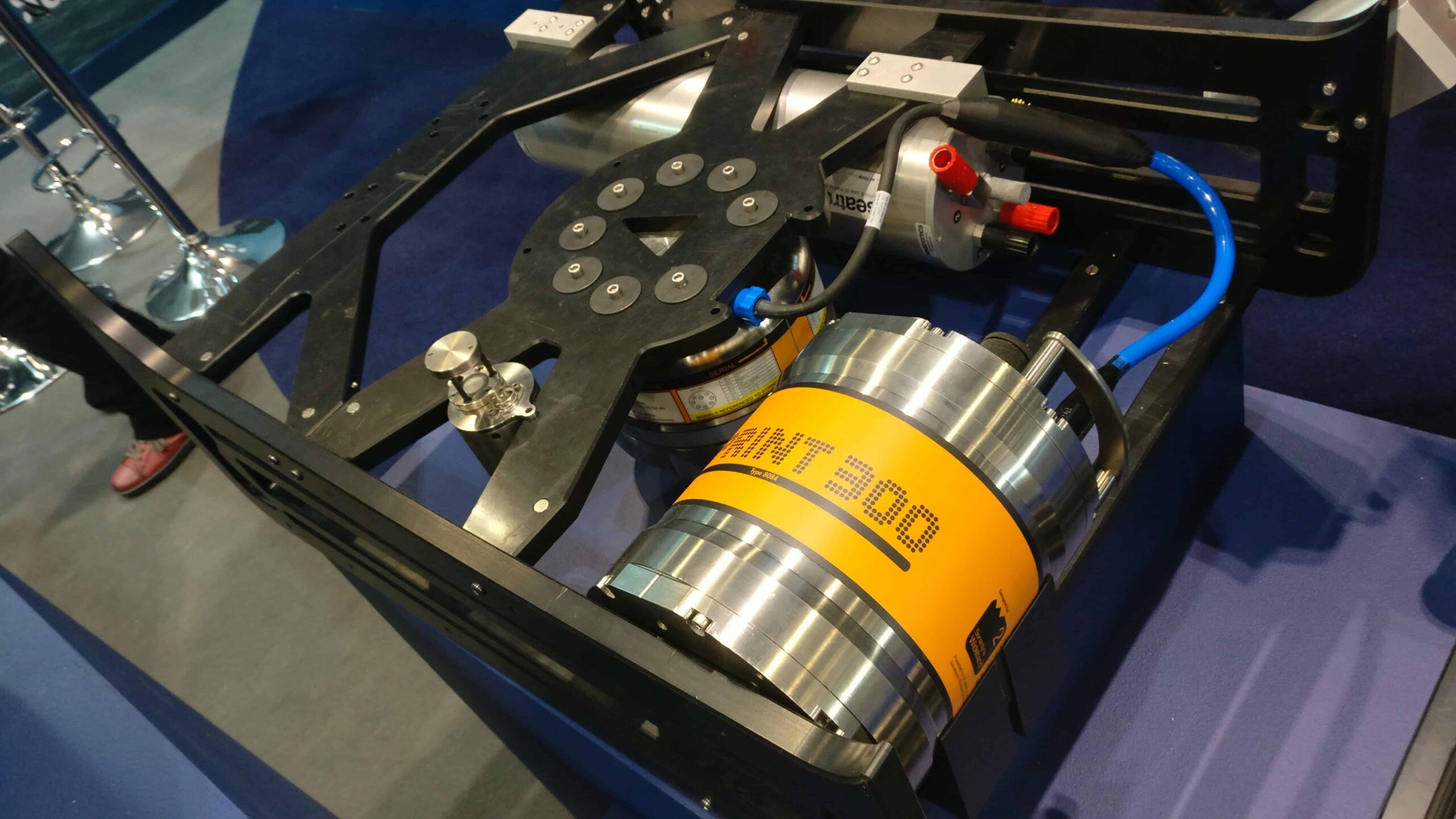
Our SPRINT 300 and Syrinx DVL fitted to the Seatronics VALOR skid for laser mapping
Leading up to the show, Sonardyne did some great work with Seaeye’s Leopard integrating our SPRINT-Nav. During OI many people showed interest in that integration. They wanted to find out what the combined INS/DVL can do for them. How does an INS and DVL combo add value to their robots? An ROV equipped with SPRINT-Nav is transformed. With SPRINT-Nav, it can be programmed to precisely hold station, to follow waypoints, to move at a constant speed. The data it gathers also increases in value as it can be accurately geo-referenced. With the right configuration and the right aiding sensors we can even perform dynamic laser mapping surveys. There’s an appetite for more capable robots in a progressively smaller form factor. New instruments and very clever manufacturing of ROVs are providing some substance to keep that appetite satisfied.
But the large work-class systems have not been forgotten. They can carry a substantial load. They can fit instruments that add value. Guess what? They are fitting them. It’s been a good year for INS sales. Our SPRINT is built on Ring Laser Gyro technology that offers a level of accuracy like no other gyro technology. It makes it ideal to help find North in record time – meaning no time lost to costly calibration procedures. It is also complimented brilliantly by Syrinx, a DVL which was born rugged and ready to withstand any subsea environment. The two systems together have seen a bumper year. At a time when ROV sales are down, savvy customers know that more capability translates into valuable data and operational savings.
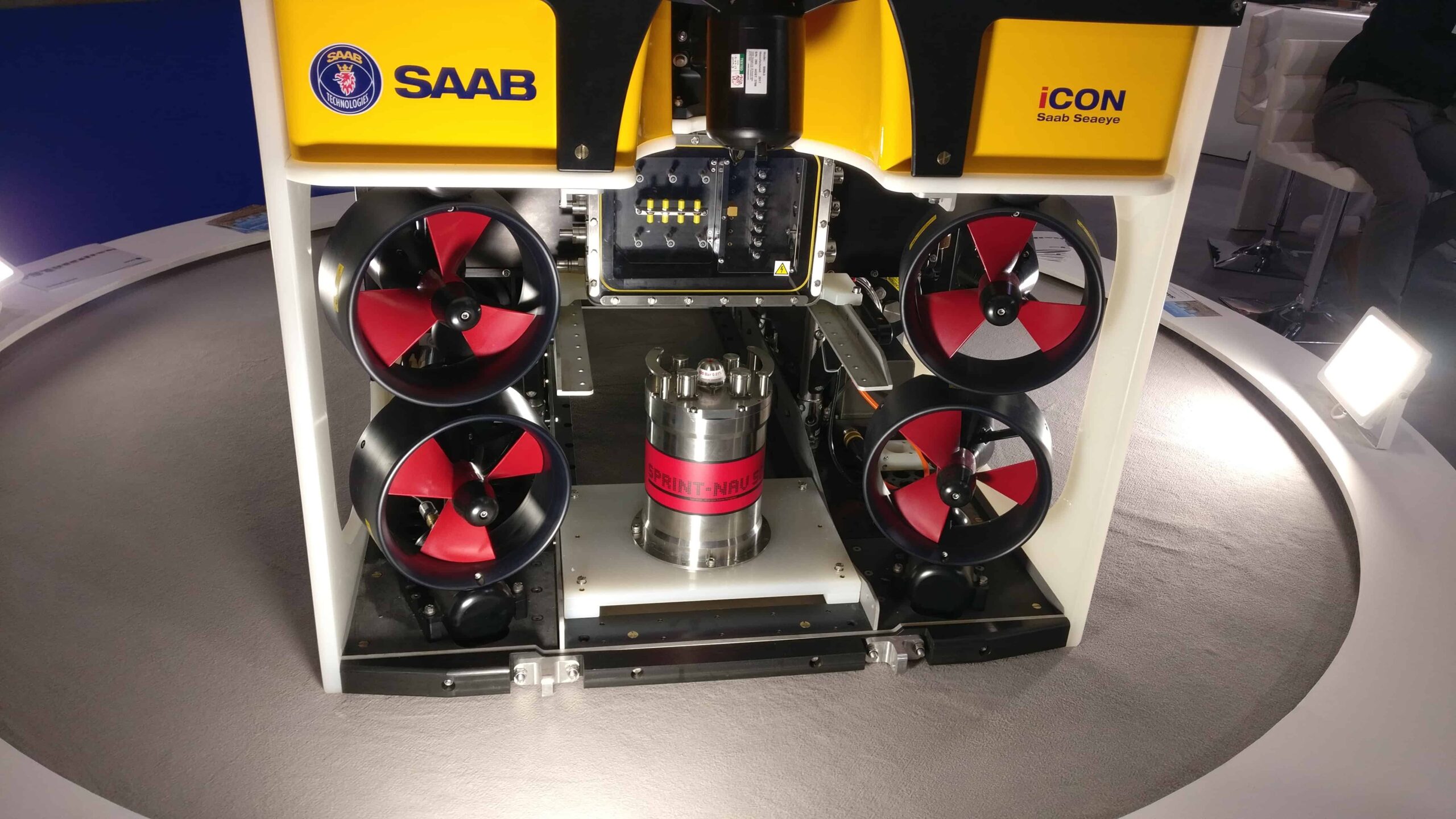
SPRINT-Nav 500 fitted to SAAB Seaeye’s Leopard ROV at Oceanology
Time for greater autonomy
When it comes to data, AUVs take the biscuit. They are very stable and can gather data at the sweet-spot for their payload sensors. Our Solstice Multi-Aperture Sonar can take advantage of that to generate amazing imagery of the seabed over a 200 meter swath. In the last six months we have been working hard with manufacturers and software companies to help them through the installation process. Soon we will be able to share some of the successes. However, beautiful data is just that: beautiful data. Valuable data is data which is georeferenced and timestamped. We need to know where it was gathered and when it was gathered. That’s when we can start to make sense of the data and what it means to us. For AUVs that has always been challenging, but we are improving. At this OI I was blown away by quality and ideas put forward by the XPRIZE finalists.The finalists were officially announced on the last day of the exhibition and their solutions where shared publicly through some of the talks. Two key themes were discussed: Innovation and a razor sharp focus on accuracy. From Arggonauts integrating our SPRINT and Syrinx to teams that are pushing 6G acoustics to the limit, I am hopeful that we will see them make a significant impact.
At the show we met with Kraken Robotics, who now operate the Thunderfish equipped with SPRINT-Nav, and their feedback has been very encouraging. Other manufacturers have also expressed interest on our Ring Laser Gyro approach. This is because when it comes to AUVs small improvements in navigation accuracy translate into massive gains in operational outcomes.
And following from our launch of Nano AvTrak 6 OEM last year at Ocean Business I am happy to report that we are now working with numerous manufacturers of small AUVs, accurate position updates are not limited to their bigger cousins.
Gateway to the Unmanned Oceans
We can count on Unmanned Surface Vehicles (USVs) to link the AUVs with the surface. In the future we will be able to conduct over-the-horizon operations with USVs linked to shore via satellite and AUVs linked to USVs via acoustics. If you stopped by our dockside demo you would have seen the C-Cat 3 from ASV demonstrating that concept. With the right tools a single USV could control a swarm of AUVs, at Sonardyne we have developed the acoustic tools to make that happen. But, it’s not just AUVs, need to box-in an LBL field? We have been doing that with ASV since 2015. It’s a commercially available solution that could have a real impact on lowering field development costs.
With our friends at Liquid Robotics, a Boeing Company, we are also doing some incredible work. They are using our acoustics to harvest data from subsea nodes at thousands of meters of depth in support of scientific operations. This concept was discussed at length on their booth. Together we are helping scientists understand the movement of tectonic plates with centimetric precision. This is something which we could only just dream about just a few years ago.
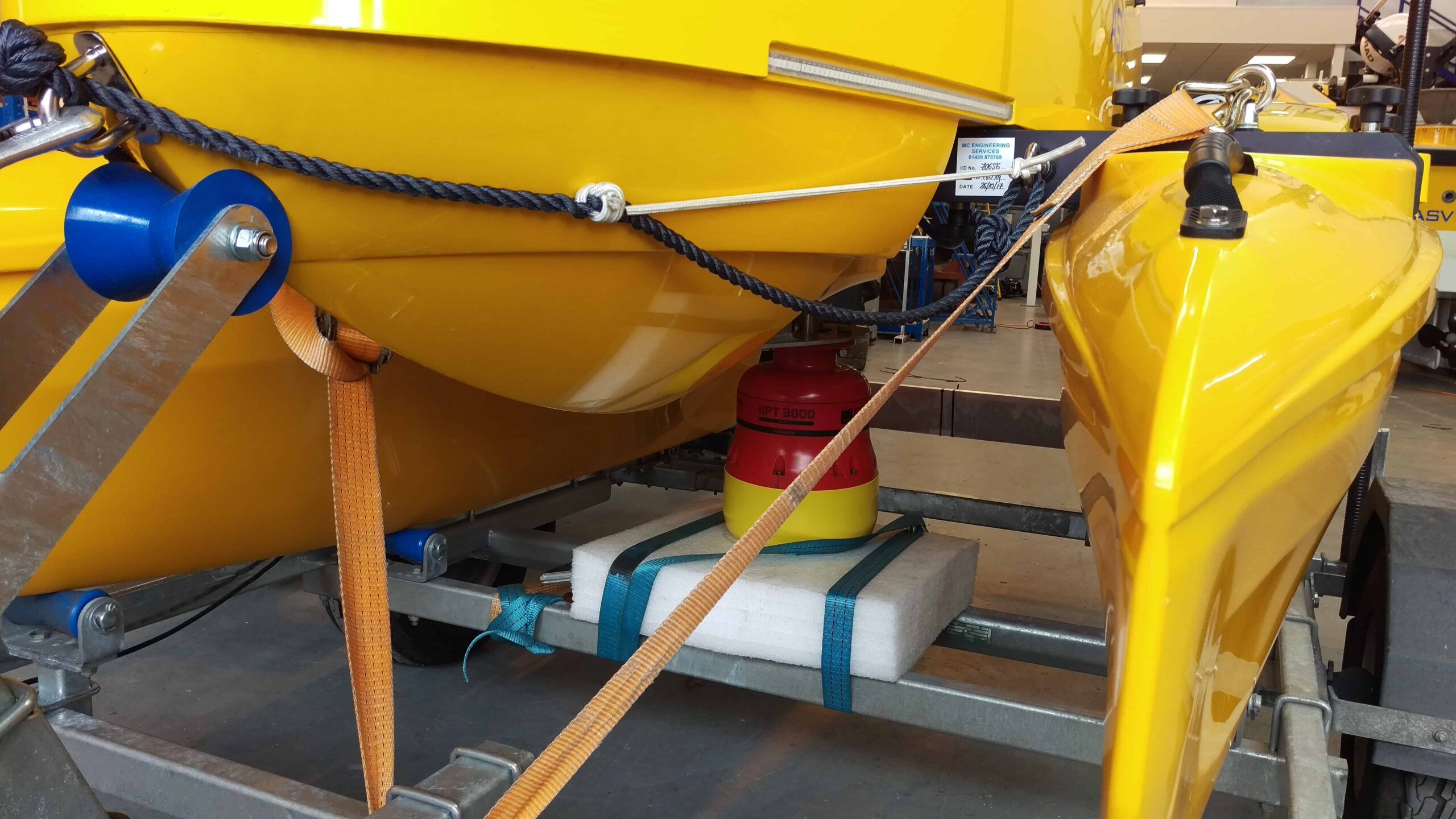
ASV C-Cat 3 with HPT 3000 USBL payload
Hybrid solutions for hybrid robots
The other stark realisation is that it’s horses-for-courses, in other words robots are being customised to serve a purpose. Yes, generic robots still exist and do well, but custom robots are now a common sight. Saab’s Sabretooth has been leading the charge for a long time now. It can work as an ROV and it can work as an AUV. Ideal for long deployments in an oil field, it can operate from a garage. It uses our 6G acoustics to guide itself in the field. Our 6G acoustics make a lot of sense as they are proven in a multitude of AUV deployments at all ocean depths and they can interact with 6G beacons and our 6G USBL systems. For developers this is a blessing. Their AUV becomes really easy to integrate into green and brown fields. It also uses our BlueComm free space optical modems to transfer large volumes of data and provide real-time joystick control even when there is not a tether linking it to a ship on the surface. They are not the only ones, Cellula Robotics are developing a new hybrid concept and also used BlueComm successfully to transfer data wirelessly.
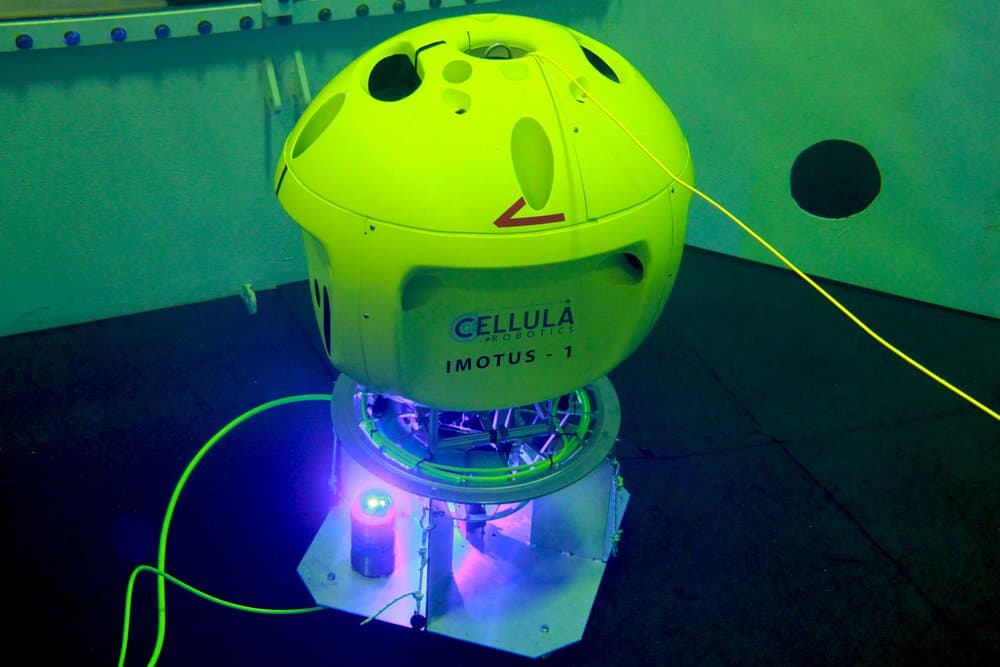
Cellula Robotics using BlueComm wireless communications
Subsea technology company, Sonardyne International Ltd, has today unveiled its smallest ever underwater target tracking system, Micro-Ranger 2. The move was made on the opening day of the Underwater Intervention conference and exhibition in New Orleans where the company is showcasing its diving and marine robotics product line-up.
Micro-Ranger 2 is Sonardyne’s third Ultra-Short Baseline (USBL) acoustic tracking system to be built around its Sixth-Generation (6G) hardware and Wideband 2 digital acoustic technology platform. But whereas Ranger 2 and Mini-Ranger 2 are designed for complex and deep water survey and positioning operations, the new entry-level model in Sonardyne’s USBL family introduces features that make it ideal for supporting diving and small vehicle operations in rivers, lakes and coastal waters.
In this sector of the market, users often have no prior experience of acoustic tracking technology so ease-of-setup and ease-of-use have been key areas of engineering focus during the development of the new Micro-Ranger 2. The system’s transceiver, MRT, is extremely small and light and can be deployed from the side of a small boat, pontoon, or even a USV. Its design provides all-round acoustic tracking coverage, so is ideal for tracking targets in shallow water all the way to the surface.
Users then simply need to connect their computer and external GPS signal to the system’s interface unit and attach a transponder to each target they want to monitor the position of. With the transceiver lowered into the water, tracking can begin.
Sonardyne is including in, the base price of the system, one of its popular Nano transponders. Measuring just over 150mm tall and weighing 225 grams in water, Nano can be fitted to a diver or small AUV without noticeably affecting dynamics through the water. A built-in depth sensor aids USBL positioning accuracy and a rechargeable battery provides a day of continuous use. For tracking larger targets, Micro-Ranger 2 can be specified with a WSM 6+ transponder which is able to be powered directly from a vehicle to provide uninterrupted tracking.
As standard, the bundled software comes with many of the powerful features common to the established Ranger 2 USBL product family. To unlock further capability, the optional Marine Robotics software pack allows users to both track, communicate and command an underwater vehicle fitted with a Nano AvTrak 6 transceiver.
Speaking at the launch, Ioseba Tena, Global Business Manager for Sonardyne said, “We’re confident that Micro-Ranger 2 will quickly establish itself as the price and performance benchmark for underwater tracking technology in its class, and prove a worthy successor to the Sonardyne Scout USBL it supersedes.” He added, “It’s great to be here in New Orleans with diving contractors and vehicle owners and operators from across the Gulf Coast states, introducing them to our very latest technology that can improve the safety and efficiency of their underwater operations.”