Why is Solstice different from other side scan sonars?
Solstice is a Multi Aperture Sonar (MAS) which functions like a top performing traditional side-scan sonar but it is processed very differently. In this approach, the multi-beam input from 32 elements is dynamically focused to extend the focus along the whole length of the swath. By using multiple apertures, the data is further enhanced and the Signal-to-noise Ratio is improved. Additionally, the Solstice array has been designed to suppress multi-path effects and improve the highlight and shadows that are critical to detect and classify objects. The overall process generates narrow (0.15°) along-track beams and boasts an impressive 200 metre swath. It’s been designed to work best when mounted on an AUV and it draws very little power.
An AUV with Solstice sees further and at higher resolution than traditional side-scans. However, compared to Synthetic Aperture Sonar (SAS) it’s shorter range and it offers less resolution.
So why SWAP from SAS to MAS?
When building AUVs, compromises have to be made. There’s a limited Space, Weight And Power (SWAP) budget. For very long endurance, ship replacement systems whose primary mission is to survey, using SAS makes sense. It can “plough” away and draw 100s of Watts, a small dent for an extra-large AUV, a massive drain on most conventional low-logistic AUV systems. That is because popular two-person portable systems have strict SWAP budgets. Even the smallest SAS systems demand twice, and even three times, more power than the Solstice. These SAS systems are also large and heavy. Fitting them on a 9” diameter AUV is virtually impossible. Even on larger AUVs, their footprint is such that operators must compromise on overall mission endurance. Fitting a SAS means less “SWAP” for your other instruments!
This is where Solstice’s MAS solution excels. It draws an incredibly low 21 Watts (including data acquisition) – which makes it equivalent to the class leading AUV side-scan sonars – but it offers a range and accuracy like no other side-scan sonar. The precision of the sonar over the initial 50 meter swath is as stunning as the leading SAS systems. At 75 meter range the precision is better than two times that of the closest side-scan sonar and unlike those competitors, Solstice is capable of providing data over a 200m swath (100m range on each side!). For a sonar that offers interferometry and motion compensation, it’s tiny and light and makes it ideally suited for a two-person portable threshold.
This means that MAS is ideally suited for rapid, low-logistics, long endurance, high resolution deployments on AUVs capable of operating from vessels of opportunity by small crews. In other words 95% of AUVs working on the Littoral!
So next time you are considering what side-scan sonar to fit on your new AUV, think MAS and get in touch with the team at Sonardyne.
Author: Ioseba Tena – Global Business Manager – Marine Robotic Systems
Marine technology specialists, Seatronics, an Acteon company, has increased its investment in Sonardyne hybrid navigation technologies following the purchase of four SPRINT Inertial Navigation Systems (INS) and four Syrinx Doppler Velocity Logs (DVLs).
The significant equipment investment, which also included six ROVNav 6 acoustic transceivers, will be added to Seatronics’ existing SPRINT rental pool in Aberdeen from where it will be made available to support oil and gas field development projects across the globe.
Introduced onto the market over 10 years ago, Sonardyne’s SPRINT makes optimal use of acoustic aiding from data sources including USBL, sparse LBL and DVL and pressure sensors to improve the accuracy, precision and reliability of subsea vehicle navigation.
Seatronics will take delivery of Sonardyne’s third generation SPRINT platform which supports dual gyrocompass and inertial navigation operating modes, allowing vehicle pilots and survey teams to utilise its navigation output simultaneously. The 4,000 metre depth rated titanium housing is smaller and lighter than previous generations providing operators with valuable payload savings whilst the power pass-through feature helps simplify vehicle integration and wiring.
The Syrinx DVLs purchased are able operate at altitudes up to 50 percent higher than conventional 600 kHz DVLs with the high resolution performance of a 1200 kHz DVL, all whilst navigating over undulating and challenging terrain of any type.
They will complement the SPRINTs by providing tight beam-level aiding to deliver unprecedented positioning performance, even if one or two DVL beams become unavailable. Co-locating plates supplied as part of the contract allow for the two units to be mated and pre-calibrated prior to mobilising equipment offshore. If needed, the units can be uncoupled, used independently, then re-connected and still be considered calibrated such is the precision of the Sonardyne co-locating arrangement.
“The purchase announced today follows the initial investment in SPRINT Seatronics made last year,” said Scott Gray, UK General Manager at Seatronics. “In that time, we’ve seen significant utilisation for the hardware and a rise in the number of project specifications calling for Sonardyne’s hybrid approach. We consider now to be the right moment to increase our inventory levels in readiness for a positive 2018.”
[blockquote author=” Paul Griffiths, Sales Manager at Sonardyne”]”Whether in the form of the co-located units purchased by Seatronics or as a single instrument, SPRINT-Nav, our all-in-one approach to subsea vehicle navigation delivers performance that’s as good as a fraction of a metre over many kilometres travelled. This translates to projects being completed in less time and for less cost. Seatronics is a long term commercial partner and we are confident they will quickly begin to see a return on their investment.”[/blockquote]
HYPACK, a Xylem brand, has announced that its market-leading HYPACK® MAX and HYSWEEP® hydrographic surveying packages can now be used to process and display data from Sonardyne’s Solstice side-scan sonar.
With over 10,000 users around the world, HYPACK is the most widely used hydrographic software package in the world. The addition of the Sonardyne proprietary file format to the data converter in HYPACK MAX and HYSWEEP means that HYPACK users can gather Solstice sonar data, process it through their editors and generate final products.
The data converter supports both the intensity and bathymetry data generated by Solstice. Options in the converter allow users to select full resolution side-scan, along with binned or full resolution, swath bathymetry. The resultant output file can be processed in the 64-bit HYSWEEP editor, MBMax64, for multibeam processing or in the HYPACK targeting and mosaicking program, HYSCAN, for side-scan data.
Solstice is a Multi Aperture Sonar (MAS) designed for Search, Classify and Map (SCM) and Hydrographic operations with integrated swath bathymetry. It has been tailored for low-logistic AUVs and gathers high resolution imagery that can be used for automatic target recognition, hydrography and post-mission analysis. With an along-track resolution of 0.15°, the imagery produced by Solstice is considered to be of the highest quality possible from a side-scan sonar.
The HYPACK MAX software has everything required to design a survey, collect, process and generate final products from single beam data, side-scan sonar, sub-bottom, ADCP and magnetometers. The HYSWEEP license includes the modules for multibeam data collection and processing and is required to process Solstice interferometric data.
[blockquote author=” NHarold Orlinsky, General Manager of HYPACK”]”The addition in the data converter allows folks to use our software to take full advantage of Sonardyne’s Solstice sonar. MBMax64 quickly handles the bathymetry through automated and manual filters, and interactive editing whislt HYSCAN creates the side-scan mosaic. Combined, the end result is a co-located data set that can be combined and analysed in HYPACK.”[/blockquote]
Ioseba Tena, Global Business Manager for Sonardyne added, “HYPACK has a long track record in the industry and it’s great that our customers can now count on this powerful software suite to manage their projects and generate client deliverables.”
A network of deep water acoustic sensors which for the past decade has provided coastal communities around India with early detection of tsunami waves, has undergone major refurbishment by subsea technology company, Sonardyne International Ltd., UK.
Deployed at key locations in the Bay of Bengal and Arabian Sea, the Sonardyne Bottom Pressure Recorders (BPRs) detect the characteristic changes in water pressure (as little as 1 centimetre in 4,000 metres depth) caused by an earthquake in the deep ocean. If a tsunami wave is detected, an alert message is transmitted up to a satellite buoy on the surface, from where it is relayed to the Tsunami Warning Centre onshore for comparison with recent seismic activity. If validated, a widescale alarm is raised to alert vulnerable communities.
The detection system is owned and operated by India’s National Institute of Ocean Technology (NIOT) based in Chennai, and was conceived following the deadly Boxing Day Tsunami of 2004. Each BPR is a customised version of Sonardyne’s Compatt transponder – a versatile subsea instrument that has a wide range of autonomous monitoring and measuring applications within offshore energy, survey and ocean science.
Unlike other systems that are available, Sonardyne BPRs are small and self-contained and thus easy to deploy. This, together with features such as low-power consumption, long battery life and reliable through-water communications, were key factors in NIOT’s decision to award Sonardyne the contract to supply an Indian Ocean Tsunami Detection System back in 2007.
The network of BPRs has remained in service for the last 10 years, detecting tsunami events on multiple occasions – none of which fortunately caused damage by the time they reached land. Data gathered by each unit on an hourly basis has been used by scientists to develop understanding of the deep ocean and improve tsunami prediction models across the region.
NIOT’s vessel visits the site of each sensor annually to carry out essential maintenance to the surface buoy and change the batteries inside each BPR – the deepest of which is deployed in 4,000 metres of water.
However, in reaching the 10-year anniversary, the decision was made by NIOT to recover the BPRs one at a time and return them to Sonardyne’s main service centre in the UK for refurbishment and re-certification. This work included replacing acoustic transducers, calibrating pressure sensors, replacing consumables and updating PCB firmware to the latest specification. All BPRs have now been returned to the field, equipped to provide many more years of reliable service.
Speaking about the performance of the Sonardyne BPRs and the contribution they have made to the international science community’s understanding of tsunamis, Dr. Venkat, NIOT Project Director, said:
[blockquote author=” ]”What started as a concept just after the 2004 tsunami incident, has matured to be a reliable scientific aid to the human race by providing reliable data and robust communication between the seabed and the deep ocean buoys.”[/blockquote]
At a recent meeting of the World Metrological Organization and UNESCO in Geneva, Dr. Venkat was awarded a Certificate for Outstanding Service in recognition of the contribution he has made to promoting tsunami detection standards in Asia.
Daniel Tan, Regional Sales Manager for Sonardyne in Singapore said, “the organisation was proud to be associated with the achievements of Dr Venkat and all the team at NIOT for the past decade.”
For more information on tsunami detection systems, click here.
Deep BV, a Dutch survey company specialising in hydrography, marine geophysics and oceanography, has purchased underwater acoustic technology supplied by Sonardyne International, UK, to support its inshore, harbour, coastal and offshore activities.
The two Mini-Ranger 2 Ultra-Short BaseLine (USBL) tracking systems and WSM 6+ mini transponders were delivered to Deep BV’s headquarters in Amsterdam within days of the order being placed and put straight to work during an operation to search for unexploded ordnance (UXO).
Mini-Ranger 2 boasts a number of features that makes it ideal for underwater operations such as UXO surveys which require high accuracy positioning but without the cost and complexity associated with a deep water USBL solution. It can simultaneously track 10 targets at very fast update rates, it is quick to install on small vessels and has a tracking range of 995 metres, extendable to 4,000 metres.
For its first project with Mini-Ranger 2, Deep BV installed one of the systems onboard their 15 metre, twin hull research vessel, Deep Volans, and configured it to track a WSM 6+ transponder mounted on a remotely operated towed vehicle (ROTV) named Iron Lady. Accurate positioning is paramount for the Iron Lady’s control software in order to ‘fly’ the six metre-wide, gradiometer UXO set-up just two metres above the seabed.
[blockquote author=” Klaas Visser, Chief Technology Expert at Deep BV”]”We’ve been a user of Sonardyne’s pre-generation Scout USBL system for several years and pleased with the results it’s delivered. However, now was the right time to replace these systems and upgrade to Sonardyne’s 6G product family with all of its attractive features and performance gains.”[/blockquote]
Speaking about the contract, Sonardyne Sales Manager, Alan MacDonald explained that Mini-Ranger 2 is ideally suited to the type of work carried out by Deep BV. “For example, the transceiver that’s used to track transponders can be mounted alongside the multi-beam system in the moon pool of the Deep Volans. Then afterwards, it’s simple to move it to a different vessel. And thanks to its excellent noise rejection properties, the system’s optimised to provide reliable tracking in shallow water, near the surface where vehicles such as Iron Lady operate.”
For more information on Sonardyne Mini-Ranger 2 USBL, click here.
Author – James Barnett. INS System Engineer
When our engineers came to select the ring laser gyros (RLGs) and accelerometers for our hybrid acoustic inertial navigation product family, inertial sensor manufacturer Honeywell was at the top of the list.
Each SPRINT uses three Honeywell GG1320AN digital RLGs and three QFLEX accelerometers. Honeywell began production of the GG1320AN digital ring laser gyro in 1995. Since then, more than 350,000 RLGs have been produced for a broad range of applications.
Out of this world performance
The GG1320AN today is the standard navigation gyro in almost all commercial air transport and business aircraft. It is also utilised on many defence aircraft and surface vehicles, including high shock/vibration systems. In addition, the GG1320AN is used for launch vehicles and satellite navigation; the recent Rosetta spacecraft to the Comet 67P/Churyumov-Gerasimenko was guided by Honeywell’s 1320AN-based system.
15 years of field data
But just how reliable are GG1320AN sensors? Well to find out, Honeywell initiated a life program more than 15 years ago. Since then, extensive analysis of gyro field data has been carried out and a detailed physics life model has been developed for the GG1320AN. Much of the field data is based on civilian aircraft usage where gyros are operated for extensive periods of time in a somewhat determined temperature environment.
Based on this fielded data, as well as life data taken on in-house gyros under long term test, Honeywell are confident that GG1320AN RLGs produced today will have lifetimes, on average, of greater than 100,000 hours when operated at approximately 40°C or lower.
Civilian aircraft usage of GG1320AN has also given Honeywell an excellent opportunity to measure the random failure rate (different from longevity or wear-out life) of gyros in inertial systems. A recent analysis of commercial aircraft supports a mean time between failure (MTBF) in excess of 400,000 hours for the GG1320AN to complement the > 100,000 hour lifetime.
Like Sonardyne, sensor life is a parameter Honeywell is focused on. With the GG1320AN, the company has confidently state life simply because of the number of devices in the field – something that many of their competitors cannot claim.
Often, inertial sensor life claims are based on component testing and then extrapolating to the sensor itself (e.g. testing optical components such as fiber, or light source, or couplers for a FOG). However, based on their own experience with RLG, IFOG (Honeywell build IFOG products for the Space trategic markets) and MEMS inertial sensors,
Honeywell consider that extrapolation of component life studies to the sensor itself is somewhat risky.
We also use the QFLEX accelerometer inside SPRINT. An equivalent of which is supplied by Honeywell for commercial aircraft with the number of fielded devices being very similar to the GG1320AN devices.
At 436,000 hours, MTBF for the QFLEX accelerometer is equally impressive with very few returns of accelerometers being seen over the life of an aircraft – typically 25 years. These sensors provide an unparalleled mix of technical performance, proven reliability & longevity and low cost of ownership from aerospace to subsea.
So next time you’re on flight, remember that the sensors helping to navigate your aircraft, are also perfect for flying your subsea vehicles.
Subsea inertial navigation technology supplied by Sonardyne Inc., Houston has been selected by the Monterey Bay Aquarium Research Institute (MBARI), for its deep-rated remotely operated vehicles (ROVs), Ventana and Doc Ricketts.
The SPRINT systems will be used in conjunction with MBARI’s existing Sonardyne Ranger 2 acoustic tracking systems to improve the accuracy, precision and integrity of subsea vehicle positioning in water depths up to 13,000 feet. The SPRINT for Ventana has already been installed and commissioned whilst the unit ordered for Doc Ricketts is scheduled to be delivered in the coming months.
Located in Moss Landing, California, MBARI is recognised as a world centre for advanced research and education in ocean science and technology. To support its work, it has at its disposal a wide range of marine technology and assets including Ventana and Doc Ricketts and the research ships which serve as their support vessels, Rachel Carson and Western Flyer.
Now in its third generation, SPRINT’s high-grade inertial sensors make optimal use of acoustic aiding from data sources including USBL, LBL and Doppler Velocity Log (DVL) and pressure sensors to extend operational capability and improve vehicle control. Uniquely, SPRINT supports dual gyrocompass and INS operating modes, meaning that ROV pilots and science teams are able to rely upon its output simultaneously. Its small, lightweight titanium housing provides valuable space and weight savings that can instead be used for additional payload and samples.
Commenting on the order, Kim Swords, Senior Application Engineer at Sonardyne said that it was further recognition of the many operational benefits SPRINT brings to international ocean science programs.
[blockquote author=” Kim Swords, Senior Application Engineer at Sonardyne”]”The need for both accurate and multiple means of subsea navigation is a priority for all missions involving marine robotic platforms. SPRINT has been helping to do this now for more than 10 years, delivering class-leading performance that helps strengthen the value of the observations and data gathered by ROVs and AUVs.”[/blockquote]
Terrestrial mapping was revolutionised by aerial LiDAR. Using high-accuracy, post-processed GNSS-aided inertial navigation for geo-referencing sensor frame point measurements into ‘real world’ coordinates has enabled reliable mapping of large areas to high accuracy extremely quickly and cost effectively. Our SPRINT-Mapper technology now provides users with a similar subsea capability and set of advantages. Simon Waterfield, Survey Support Group Manager and Dr Mikael Larsen, Principal Engineer – INS, explain how the system’s concept, features and exhaustive testing regime now has the capability to deliver subsea mapping to centimetre – level accuracy and resolution from a dynamic vehicle.
Underwater mapping surveys can be broadly divided into two disciplines; mobile and static.
Up until now, mobile mapping efforts largely involved multi-beam sonars being fitted to ROVs and AUVs alongside a spread of INS, DVL, acoustics (e.g. USBL) and depth instrumentation. Being dynamic, large areas can be quickly imaged but at best, this approach can only achieve up to ~10cm relative accuracy – ruling out any applications that require centimetre or better accuracy.
Over the last few years, subsea LiDAR and laser/camera optical mapping sensors have emerged with resolution and accuracy at the millimetric to centimetric level. These sensors have most commonly been used to scan from a static location (e.g. a tripod or ROV resting on the seabed). Due to the relatively short and variable optical range (limited by turbidity), multiple scans are often required. This involves relocating the scanner and eventual artificial targets needed for stitching individual scans together in – a process called ‘point cloud registration.’
However, static scanning from the seabed inherently limits the perspective to a horizontal view only whilst relocating the scanner, waiting for sediment to clear and lengthy processing time, adds considerable time to any survey – and offshore time is money.
Mobile mapping – the wide area navigation challenge
But what if you could combine the operational efficiency of wide area mobile mapping with the precision of static mapping?
Well, with the arrival of our SPRINT-Mapper now you can. It provides tightly integrated acoustically-aided inertial navigation matching the resolution of state-of-the-art optical mapping sensors, and is the latest major technology milestone in an INS research and development program that spans more than a decade.
The level of practical positioning accuracy is unprecedented and a true enabler for wide spread use of high tempo subsea mobile mapping projects. It provides enough redundancy and QC to both reliably satisfy accuracy requirement and support high-integrity applications such as spool-piece and jumper metrology.
By adopting a dynamic platform, such as an ROV navigated fitted with our SPRINT INS, Syrinx DVL and Fusion 6G (sixth generation) LBL acoustics, a site can be mapped much quicker with much less issues from reduced visibility as the ROV does not have to come into contact with the seabed at the survey site and can move to scan any target of interest. For metrology operations, the ability to dynamically position a laser in close proximity to the structures allows operations to be conducted in reduced visibility, reducing delays, and allowing a greater point density over targets. High resolution point cloud data can contain a wealth of information which can be utilised for various applications.
Whilst contactless subsea metrology is one of the obvious applications, the ability to generate geo-referenced 3D maps at the centimetric accuracy level supports a wide spread of applications also including; structure mapping, pipeline inspections, mooring chain surveys, inland waterway inspections, scour surveys, seabed coral/ fauna mapping, wreck and drilling mud surveys to name a few.
What makes up the system?
A typical 3D mobile mapping campaign involves equipping a subsea vehicle – be it ROV, AUV or manned-submersible – with a pre-calibrated SPRINT INS co-located with a Syrinx DVL (or our new combined SPRINT-Nav), ROVNav 6 transceiver, high-precision depth sensor, sound velocity sensor and your choice of high resolution laser/camera, LiDAR or multi-beam.
Compatt 6 transponders such as the new Micro model, are deployed on the seabed around the survey area with their approximate relative positions to each other reliably and time efficiently determined by DVL/INS dead reckoning. The vehicle then carries out the required survey of the structure, while the INS, DVL, LBL ranges, depth and sound velocity are gathered by the SPRINT and Fusion software. The process does not require transponder-transponder acoustic line of sight, but can utilise these acoustic baselinemeasurements when available.
On completion of the survey, the raw sensor data is post-processed using our powerful software tool, Janus. Post-processing concurrently calibrates transponder positions using a SLAM (Simultaneous Localisation and Mapping) technique and optimises absolute and relative navigation accuracy. The finished navigation data is then merged with the laser/ camera, LiDAR or multi-beam data to produce a geo-referenced 3D point cloud.
Our factory-supplied equipment is the latest specification and preconfigured to ensure your operation can be mobilised as quickly as possible. In the planning phase of a project, the expert knowledge of our Survey Support Group (SSG) is available to help you plan every aspect of the operation including reviewing procedures and tasks to identify and reduce risk ahead of mobilisation. Highly experienced Sonardyne personnel will then join your offshore survey team to operate the acoustic and inertial system, gather the required navigation data and post-process it offline.
Here’s some of the technical benefits of SPRINT-Mapper for dynamic mobile mapping.
• The ability to aid SPRINT with tightly coupled Fusion 6G two-way travel times, with each range received individually
• The ability to combine individual Syrinx DVL beam velocities rather than generic DVL instrument frame velocity and thereby operate robustly over structures and where DVL beam slant ranges dramatically differ.
• All 6G acoustic aiding (LBL and DVL) uses rich proprietary quality metrics, and timing is guaranteed to the micro-second level.
• System architecture has been designed to remove the risk of issues with latency or timing jitter on ROV MUX communications to topside, which could affect time synchronisation between instruments when receiving 1PPS from topside, as per established methods.
• Janus post-processing software is an extremely powerful tool for ensuring the very highest quality post-processed navigation with full QC of data. It performs forwards and backwards post-processing of the INS data and utilises a host of other proprietary techniques to optimise system performance in every operational scenario and condition.
So what performance can you expect to see? Well, our approach delivers the following 3D point cloud tolerances;
• 1cm level typical accuracy (vertical and horizontal baseline RMS) for single run-line distances of ~20m (typical metrology) and not much worse over longer distances.
• 5-10 cm level typical area (e.g. 50-200m square) mapping accuracy when merging multiple run-lines at arbitrary headings.
Track record
For the past three years, we’ve been working behind the scenes supporting clients with their mobile mapping projects, witnessing firsthand how this game-changing capability can re-write the operational rule book.
MBARI Deep water ROV mobile mapping trials were first performed in 2014 and then again in November 2015 onboard the R/V Western Flyer through co-operation with the Monterey Bay Aquarium Research Institute (MBARI). A conventional Compatt 6G array was deployed and calibrated to act as reference for the mobile mapping trials. The reference acoustic baselines were compared to the 3D point cloud derived baselines. The difference ‘C-O’ RMS between the baselines was just over 3cm with a single baseline error marginally above 5cm. Additionally, simulated flange/hub assemblies were mapped and demonstrated angular accuracy robustly below 0.5 degrees. Baseline Issue15 has the full article.
UTEC/McDermott Following these successful trials, Sonardyne and laser manufacturer 2G Robotics were invited to perform a contactless dynamic metrology trial by UTEC and McDermott in a deep-water operational environment. The operational elapsed time and results were compared to a static laser metrology and delivered on the requirements of meeting typical metrology tolerances whilst delivering operational efficiency and cost savings.
Further operational projects followed in collaboration with 2G Robotics last year, including with DeepOcean and with the National Oceanographic and Atmospheric Administration (NOAA).
NOAA The project with NOAA demonstrated the versatility of the system; in this case it was installed and operated on a manned submersible to map two key archaeological wreck sites, the U-576 submarine and the freighter SS Bluefields. Even in challenging dynamic and environmental conditions, SPRINT-Mapper provided outstanding accuracy, with the condition of both wrecks, their fittings and features easily distinguished and identifiable for analysis.
DeepOcean DeepOcean’s dynamic survey operation covered 12 drill centre locations and a total of 27 metrologies, setting new bench marks for high resolution contextual3Dsurveywhile proving an alternative and rapid ‘contactless’ solution to conventional metrology surveys.
DOF Late last year, we supported DOF at The Underwater Centre in Fort William, Scotland, to demonstrate mobile mapping to invited industry representatives. The ‘truth’ reference for this trial was traditional Sonardyne 6G LBL acoustic metrologies and third-party gyro packages.
Laser results were an average of inferred metrology from two runs (in same direction). Despite the extreme weather conditions, our full program results are within metrology tolerance of the truth reference.
Tested. Trialled. Proven
The benefits of underwater mobile mapping have now been proven with ultra-fast wide area surveying, inspection and metrology. Turbidity affecting visibility can be reduced by moving the dynamic vehicle closer to the target. The use of tightly coupled Sonardyne 6G acoustics provides trusted quality control alongside optimal aiding to the INS. Mobile mapping does require a complex system integration of INS, DVL, acoustic ranges and mapping sensor to achieve centimetric results. But this is overcome with our unique, ‘under-one-roof’ capability.
We have ability to merge and post-process all sensors at the raw data level. We have a deep understanding of subsea operations and your commercial pressure. And we have experienced offshore personnel ready to support you every step of the way, de-risking your projects. This proven capability has the potential to revolutionise many subsea operations. Contact us to discuss how it could revolutionise yours.
Author: Malik Chibah – Engineering Manager
We hosted a live, in-water demonstration of our new SPRINT-Nav, acoustically aided inertial navigation system (AAINS), at our Plymouth trials facility, UK. We wanted to put our new technology through its paces, to really demonstrate why SPRINT-Nav will be the new industry leader in subsea vehicle hybrid navigation.
Our SPRINT-Nav combines high-performance INS with unique tight integration of raw, low level digital signal processing from the latest generation Sonardyne Wideband LBL and DVL acoustics, all time synchronised to the micro second level.
It wasn’t all plain sailing though. The weather was against us, and the environmental conditions around Plymouth are testing at the best of times. DVL performance in particular is adversely affected by the poor sea state as there was excessive acceleration for the DVL itself at the bottom of the pole due to the large pitch and roll of the vessel and increased aeration in the water. However, SPRINT-Nav still performed with outstanding results, which is a real testament to the robustness of this system.
Our equipment and set-up
In order to conduct our demonstrations, we took the following equipment with us; SPRINT-Nav mounted on a through-hull pole on our survey vessel to mimic an AUV/ROV. ROVNav6 LBL transceiver to provide LBL aiding to the SPRINT-Nav by ranging to two Compatt 6s, one Compatt 6 was placed at the Plymouth breakwater and one a few kilometres southwest in Cawsands Bay. An SV sensor was used to give us an accurate reading of the water sound velocity, and reference was provided by RTK GPS/GNSS with a nearby base station to give us a base to compare against.
Extraordinary autonomous performance
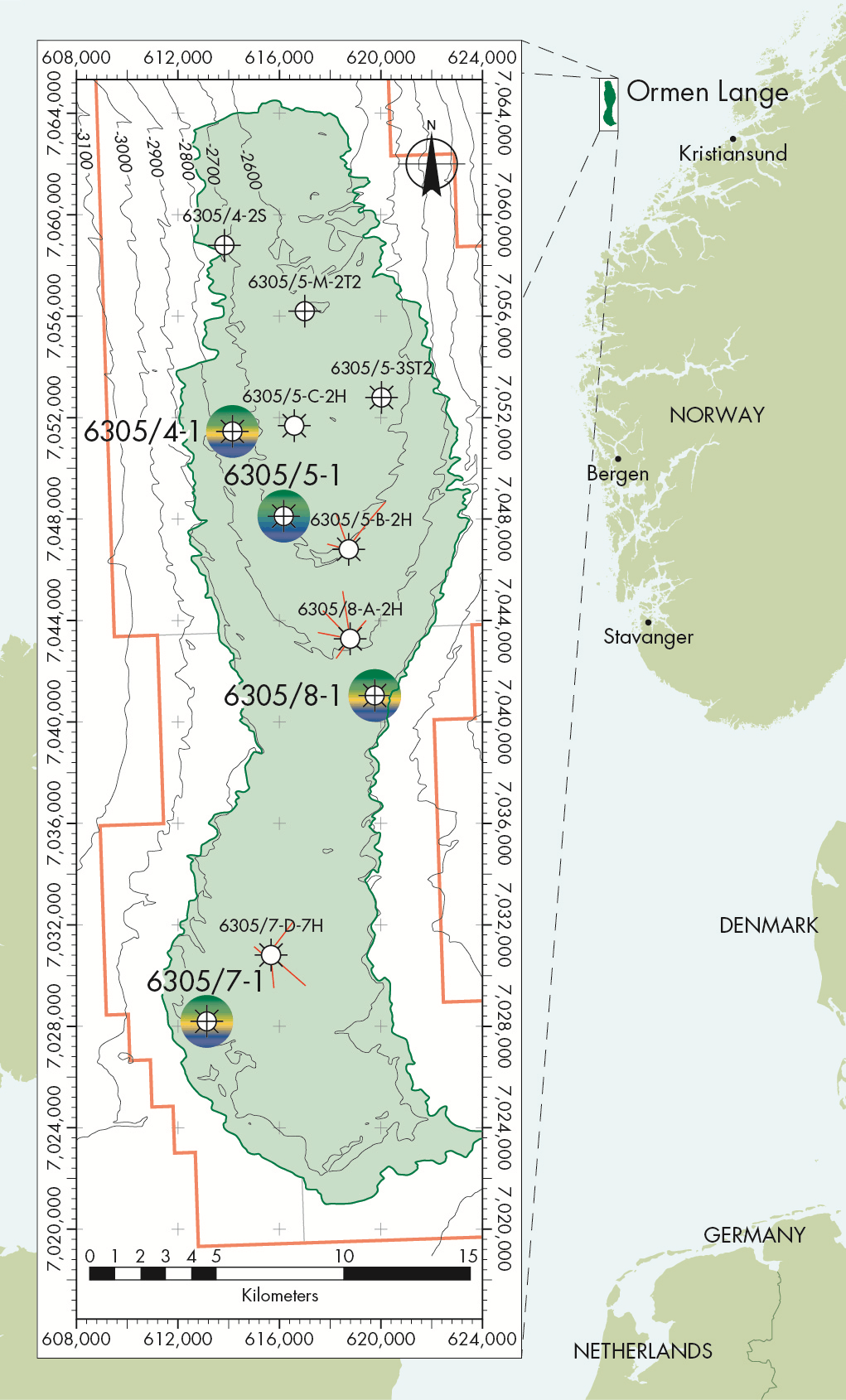
Figure 1 – DVL-INS dead-reckoning and free-inertial AUV dive runs
Despite the rough weather, and rougher sea conditions (over 2 metre high waves!), SPRINT-Nav provided extraordinary high accuracy Doppler-Inertial positioning throughout the demonstration. Observed drift was consistently about 1 meter per 2-3km of travel away from the origin. This level of practical real world performance is unrivalled in the marine industry and forms dependable core functionality for any high performance AUV/ROV.
The map (figure 1) shows all of the runs we completed using autonomous dead-reckoning based positioning, making full use of the diversity in the environment in the Plymouth Sound.
The power of three– using sparse LBL-DVL-INS positioning
We wanted to demonstrate SPRINT-Nav’s ability for tightly integrated sparse LBL. This is where the acoustic two-way-travel time measurements from the passing of a transponder en route of a linear trajectory automatically resets DVL-INS dead-reckoning drift.
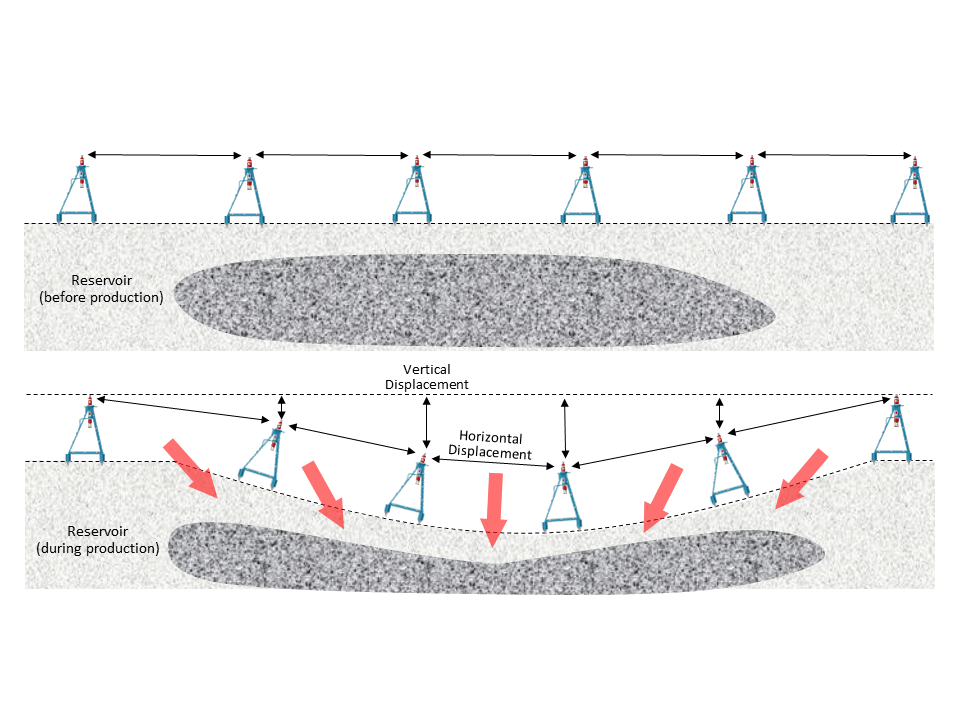
Figure 2 Single transponder sparse LBL – DVL – INS positioning
We travelled from the Mountbatten pier (NE), passing the first transponder at the Plymouth Sound breakwater after 3km and arrived at the second transponder located in Cawsand Bay (SW) after about 5.5km, see Figure 2 – transponders are indicated by bright blue diamonds.
The SPRINT-Nav LBL-DVL-INS positioning as compared to the RTK GPS reference is shown below (Table 1). Positioning accuracy was robustly within 2m at all times and reduced to << 0.5m when passing a transponder. Sparse LBL performance and range in the Plymouth Sound is severely compromised by the shallow water and highly complex and variable sound velocity profile.
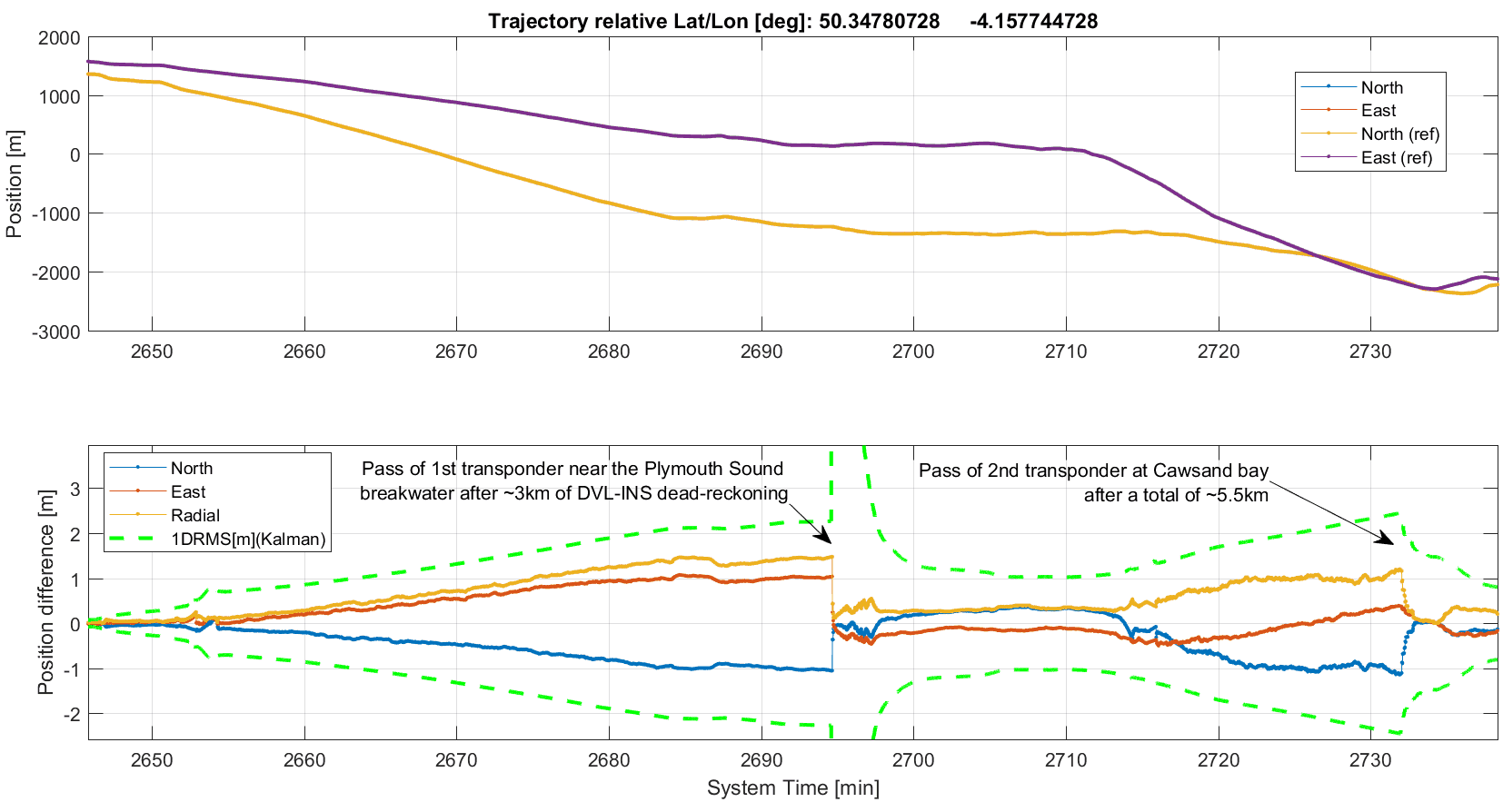
Table 1 – Wide area sparse LBL-DVL-INS vs RTK GPS reference
In a typical offshore environment the realistic transponder maximum ranging distance would be 1 to 3km and SPRINT-Nav accuracy relative to a single transponder would be ~0.1% of slant range (1DRMS), i.e. 1m @ 1km distance when the vehicle passes a transponder at a right angle. The extremely accurate SPRINT-Nav wide area sparse LBL positioning is a consequence of careful tight INS integration of Sonardyne state-of-the-art Wideband DVL and LBL acoustics.
Ultimate accuracy
In order to get the most accurate data possible, it’s necessary to perform post-processing. We have a software product called Janus (named after a Roman god that can look forwards and backwards in time, at the same time – just how the Kalman smoothing technique our software uses works) which reduces the error in the data collected. We took the data that SPRINT-Nav collected during our dive runs and processed it with Janus.
The graph below (Table 2) shows the results from Janus compared to the reference RTK GPS. Radial error is a few decimetres (RMS) and peak error towards the end of the mission is ~0.5m. This is a threefold improvement as compared to the real‑time navigation in the graph above. Often more importantly, the short term relative accuracy and precision is at the sub-mm level to centimetres over 10-100m distances.
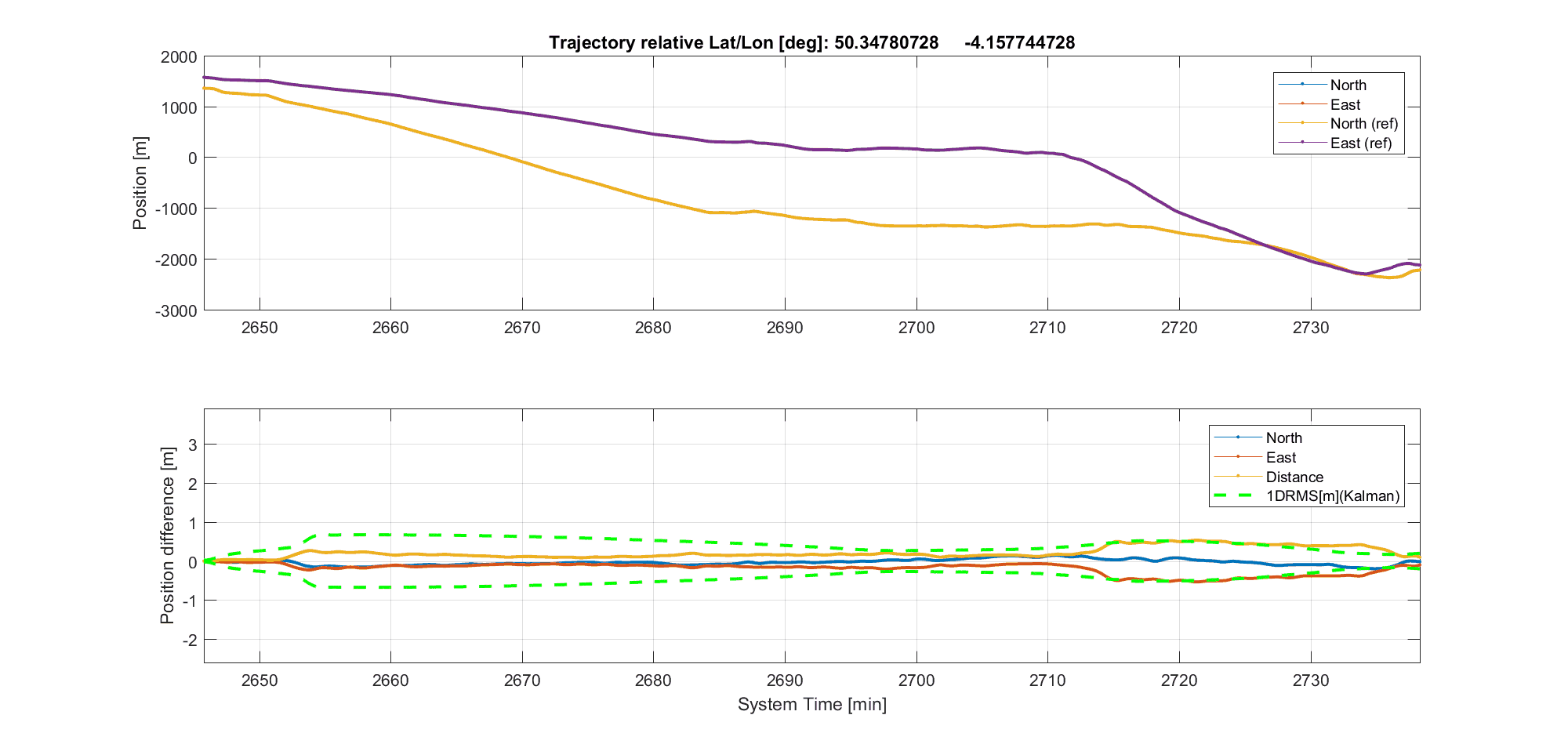
Janus post-processed wide area sparse LBL-DVL-INS
The Janus software is really easy to use. All we had to do was import the data from SRINT-Nav and click a button to perform the post-processing function.
The majority of the radial position error (0.5m) observed towards the end of the test likely stems from LBL sound velocity profile error and potentially the shallow Cawsand Bay seabed transponder experiencing a slight drift along the seabed caused by the very rough seas overnight between time of deployment and the demonstration. Peak post-processed radial position error in a real ROV/AUV operation (10km straight line from known origin with transponders at 5 and 10km) would likely be at the 0.3m level or less.
“Free inertial” AUV dive
On our way back to the marina we took the opportunity to illustrate SPRINT-Nav’s “free-inertial” capabilities. This is where the SPRINT part of the unit is working by itself, without any aiding from the DVL or GPS. The radial peak free-inertial position error was 17m over 8 minutes which reduced to 8.1m following DVL bottom lock. This level of demonstrated performance is on-par with or better than the highest performing competitive product. The key here is that the SPRINT-Nav 500 we used is not our highest performing product. So should you need a higher performing free inertial unit, our SPRINT-Nav 700 variant is the one for you.
Tight beam level DVL integration and beyond
Our final demonstration of the day was to highlight how well the tight beam level DVL integration is within SPRINT-Nav. The SPRINT INS user interface provides the ability to selectively switch off processing of individual DVL beams as a simple means of demonstrating the effect and power of tight DVL beam level INS integration. In sequence, processing of 1, 2 and finally 3 beams were switched off. Disabling of one and two beams had a hardly discernible effect on position drift – it remained at <0.25m after 10 minutes. Disabling the third beam caused a significant increase in drift rate as could reasonably be expected. The accrued position error remained below 2 meters after 13 minutes of single beam DVL-INS dead-reckoning.
There are a number of planned future updates to the capabilities of our DVL products, including allowing Syrinx to output <3 beam velocities continuously meaning that if you managed to severely damage your Syrinx DVL, you will still be able to continue with your operations, rather than having to stop until your unit is repaired and reinstalled on the vehicle.
Working throughout the night
After the demonstrations had ended, we decided it would be a good idea to test out the DVL-INS station keeping capabilities of our SPRINT-Nav. We left the unit working away, using DVL and pressure depth aiding, when we left the vessel at 5pm. We returned the next morning to see what had happened over night. In the almost 16 hours SPRINT-Nav had been running, the drift was ~1m. This is pretty impressive considering the strong currents experienced during the period. From this data we would expect SPRINT-Nav to be capable of ~1m drift in a 24 hour period in more benign ROV/AUV station keeping operations.
The time on-board our survey vessel around Plymouth provided us with some great insight into just what SPRINT-Nav is capable of, and we’re excited to see it used offshore, making a positive difference to your subsea vehicle operations.
If you would like to find out any more information about our SPRINT-Nav family, please get in touch to discuss your requirements with us.
Ocean science technology company, Sonardyne International Ltd, UK., announced today it has been awarded the contract to supply Britain’s new polar research vessel, RRS Sir David Attenborough, with subsea acoustic tracking and position reference equipment.
The Ranger 2 Ultra-Short BaseLine (USBL) system will be used by scientists to precisely track the position of, and communicate with, scientific instruments and robotic vehicles deployed from the vessel, including the now famous Boaty McBoatface AUV. Ranger 2 will also be interfaced with the vessel’s dynamic positioning (DP) system for precise station keeping during science operations.
Commissioned by British Antarctic Survey, an institute of the Natural Environment Research Council (NERC), and being built by Cammell Laird in Birkenhead to a Rolls Royce design, the RRS David Attenborough will be one of the most advanced vessels of its type when it enters service in 2019. Measuring 128 metres long and 24 metres wide, the new ship will have a range of 19,000 nautical miles and be able to accommodate up to 60 scientists engaged in ocean, seafloor and atmospheric research.
Sonardyne’s Ranger 2 will support the RRS Sir David Attenborough’s pioneering work by enabling science teams to precisely monitor the position of underwater systems deployed from the vessel. Sonardyne’s exclusive wideband acoustic signal technology and 6G (sixth generation) hardware platform allows autonomous and remotely-operated vehicles, towed platforms and seafloor landers to be simultaneously and precisely tracked to ranges beyond seven kilometres.
Alongside design and engineering services, Rolls Royce is supplying a comprehensive package of control systems and equipment for the vessel, including the DP system. This will utilise data from Ranger 2 to maintain a stable vessel position as equipment and vehicles are deployed and recovered in some of the most challenging marine environments on the planet.
Sonardyne’s contract includes the supply of two through-hull deployment machines, seafloor and vehicle-mounted tracking transponders, and topside control hardware and software. The first equipment deliveries to Cammell Laird for integration into the vessel have already begun.
The commissioning of the RRS Sir David Attenborough represents the UK Government‘s largest investment in polar science since the 1980s. When the ship comes into service, all three Royal Research Ships, James Cook, Discovery and now Sir David Attenborough, will be equipped with Sonardyne underwater positioning technology.
[blockquote author=” Mark Carter, Global Business Manager for Sonardyne”]”As a privately-owned British engineering company, it’s a great honour for our technology to have been selected for Britain’s next polar research vessel. The work now begins to deliver Ranger 2 and support Rolls Royce, Cammell Laird and British Antarctic Survey through the installation and commissioning phases of the project.”[/blockquote]
For more information on Ranger 2, click here.